AUTHOR ARCHIVES: Mark Glover
About the Author:
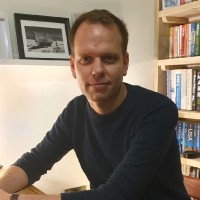
Mark is an experienced B2B editor and journalist having worked across an array of magazines and websites covering health and safety, sustainable energy and airports.
May 29, 2019 • News • Augmented Reality • future of field service • Scope AR • Software and Apps • Enterprise Working
Scope AR, the pioneer of enterprise-class augmented reality (AR) solutions, today launched at Augmented World Expo 2019 (AWE) an upgraded version of its highly-touted WorkLink platform. With the addition of session recording, WorkLink becomes the industry’s only AR knowledge platform to offer real-time remote support, access to AR work instructions and the ability to record sessions simultaneously in one application. With this, workers can now easily capture, retain and share knowledge like never before. Scope AR also announced new enterprise customer, medical device manufacturer Becton Dickinson, as well as expanded use of its integrated AR platform with Lockheed Martin.
“This is an exciting time for the AR industry. Adoption is growing and expectations among users are shifting towards more comprehensive, enterprise-ready solutions,” explained Scott Montgomerie, CEO of Scope AR. “With the latest WorkLink platform, we’ve added even more ways for workers to collaborate and quickly get the knowledge they need to successfully do their jobs. With the addition of session recording, businesses can now better capture and retain knowledge for future use and training purposes, while taking compliance, quality assurance and accuracy to the next level.”
The updated WorkLink platform can be customized with varying sets of functionality depending on customers’ needs. It can also be deployed across all major platforms and select industry wearables so organizations can use their device of choice. The platform is built to help make anyone an instant expert with seamless access to a variety of features including:
Session Recording to capture important knowledge delivered during live support video calls for retention, future sharing and new insight into additional training needs and how processes can be improved. Either the technician or remote expert can record a live session so real-time knowledge becomes a reusable asset that can be accessed by others in the future.
Beyond its latest product innovations, Scope AR has also experienced continued customer acquisition and growth on the heels of its $9.7 million Series A funding round in March 2019. Becton Dickinson, an American medical technology company that manufactures and sells medical devices, instrument systems and reagants, is the newest addition to the company’s already impressive client roster. Becton Dickinson will use WorkLink at the company’s Automation Center for Enablement to deliver AR instructions across the organization.
Additionally, Lockheed Martin is now expanding its use of Scope AR’s technology after its highly successful implementation of WorkLink to improve workforce training and spacecraft manufacturing procedures. They are now deploying Scope AR into all four of their business units across a broad variety of use cases.
Lockheed Martin’s Emerging Technologies Lead Shelley Peterson added, “Creating AR work instructions with WorkLink has enabled our Space team to reach unprecedented levels of efficiency and accuracy, as well as reduced manufacturing training and activity ramp-up time by 85%. Scope AR's platform has proven to be so valuable that we have expanded our AR adoption into even more manufacturing applications within the Space division, as well as leveraging the technology in other areas of the business."
May 29, 2019 • News • management • Cyber Security • insurance
In November last year, Mactavish published a report entitled ‘Cyber Risk & Insurance Report’, which identified eight common flaws in cyber insurance policies. This includes, for example, cover being limited to events triggered by attacks or unauthorised activity and excluding cover for issues caused by accidental errors or omissions.
Another flaw is only providing systems interruption cover for the brief period of actual network interruption, as opposed to the more significant knock-on revenue impact during the period after IT systems are restored but the business is still disrupted. In the last two weeks alone Mactavish has reviewed cyber insurance policies for a large British business and a medium sized business. Both of these policies had three or more of the flaws. Mactavish warns that despite insurance industry denials, the eight flaws are widespread.
Bruce Hepburn, Chief Executive Officer, Mactavish, commented: “Many in the industry have challenged our findings but we continue to find these issues affecting the actual policies we review that are being offered to UK businesses, and we will be publishing a second paper on the sector next month providing more details on our findings. “However, in the meantime, we are calling on brokers to challenge insurers more on the quality of the cyber cover they provide and push for improvements. If they can’t achieve this, they need to warn their clients of the omissions in their policies to give them a better understanding of what they are buying.”
Mactavish has issued a challenge to insurers and brokers to guarantee that the eight common flaws it has identified in policies will never be used as reasons to refuse pay-outs on cyber insurance claims unless they can show that a client has been informed but decided not to buy the additional cover. The eight flaws outlined in the Mactavish Cyber Risk & Insurance Report are:
1. Cover can be limited to events triggered by attacks or unauthorised activity – excluding cover for issues caused by accidental errors or omissions;
2. Data breach costs can be limited – e.g. covering only costs that the business is strictly legally required to incur (as opposed to much greater costs which would be incurred in practice);
3. Systems interruption cover can be limited to only the brief period of actual network interruption, providing no cover for the more significant knock-on revenue impact in the period after IT systems are restored but the business is still disrupted;
4. Cover for systems delivered by outsourced service providers (many businesses’ most significant exposure) varies significantly and is often limited or excluded;
5. Exclusions for software in development or systems being rolled out are common and can be unclear or in the worst cases exclude events relating to any recently updated systems;
6. Where contractors cause issues (e.g. a data breach) but the business is legally responsible, policies will sometimes not respond;
7. Notification requirements are often complex and onerous;
8. Businesses are forced to choose IT, legal or PR specialists appointed by their insurer.
May 29, 2019 • Features • copperberg • future of field service • Field Service Summit • Parts Pricing and Logistics
Would you walk into a pub that served you a warm beer the previous time? Or, go back to this fine dining restaurant with your partner if it was noisy and unclean? One word that can make or break it for the service business is ‘Experience’.
With customer satisfaction being the buzz word in the past years, now the new trending words are ‘Experience Economy’, ‘Customer Delight’, and ‘Good-feel Service’. The trend is very common in the B2C sector which has led to terms like ‘Uberized Service’, ‘Amazon like Delivery’ or ‘Disney like Experience’.
This wave of keeping customers happy and providing them with a great experience has to become a priority on the list of the majority of Field Service Directors today. With the quest to create the perfect value proposition and customer experience comes in the various challenges that these leaders in manufacturing face today.
Recently, I had a fantastic opportunity to moderate a round-table discussion along with Kris Oldland, Editor of Field Service News about the Challenges that Service Leaders Face today and the future technologies in Field Service and Spare Parts at the Spare Parts Summit Summit in Coventry, UK.
One important observation was the interlinking of issues with spare parts and field service. The service leaders faced challenges in obsolesce management, spare parts management, data collection, utilisation and analysis along with field workforce training and planning.
With the advent of digital tools, faster production and time to market, one big challenge for Service Leaders today is obsolescence management as it has become increasingly challenging to predict and prepare for the future. IoT and connected machines have made predictive maintenance easier and helped the service organisations to move into the proactive space than the reactive space. One challenge still remains with break-fix due to user mismanagement, negligence or insufficient training.
Although IoT allows companies to note some cases of misuse and offer training proactively preventing damage to the machines and need for servicing prematurely. The service leaders have accepted that there will always be break-fix with machines whether it is due to an unforeseen circumstance or a user issue. So the goal in these instances is to have enough data to be able to get a technician with the right spare parts to the location and get it fixed immediately.
"One important observation was the interlinking of issues with spare parts and field service..."
This is a shift from the older model of a technician visiting to collect information, making a fault report to get the spare parts and revisiting the customer to fix the issue which is a higher cost for the service company and loss in uptime for the customers. Tracking of spare parts and more specifically ‘Having the rights parts at the right place’ is also an issue being tackled currently by the service leaders.
Some leaders are concerned about the tracking of spare parts as they become ‘lost’ with technicians, in spare part boxes or in inventories. Technologies like RFID readers, GPS tags could play a big role in actively tracking the spare parts to make sure the parts can be delivered to the right place when required.
The manufacturing, service and aftermarket space today is in a fantastic rush for data and today is commonly referred to as the new gold or oil. Kris Oldland had an interesting take on how this gold can be dug out but will still be useless unless refined and put it in the right form. One challenge with data is also getting data from the right source.
Similar to ores to extract gold, if the content of the ore is bad, the gold will be very expensive to extract and the return on investment will be low or negative. Data has a similar proposition today. Companies have started asking, how much data is enough data and which data is good data. With better data processing, artificial intelligence and machine learning making progress, the data analysis and processing woes should be answered more effectively in the near future.
The challenges cannot be addressed with a magic wand or just ignored, but being able to address them is a progressive first step. Collaboration with the customers and getting them involved in the whole process of solving the challenges can also boost progress for the service organisations.
To sum it up according to a Forbes quote,’An experience is not an amorphous construct, it is as real an offering as any service, good or commodity.’
May 28, 2019 • News • 5G • future of field service • Berg Insight • IoT
The first 5G cellular IoT modules will become available to developers this year, enabling early adopters to create the first IoT devices based on the standard. Based on the experience of previous introductions of new standards, 5G will however not be an instant hit. By 2023, Berg Insight forecasts that 5G will account for just under 3 percent of the total installed base of cellular IoT devices.
“5G still has some way to go before it can become a mainstream technology for cellular IoT”, says Tobias Ryberg, Principal Analyst and author of the report. “Just like 4G when it was first introduced, the initial version of 5G is mostly about improving network performance and data capacity. This is only relevant for a smaller subset of high-bandwidth cellular IoT applications like connected cars, security cameras and industrial routers. The real commercial breakthrough will not happen until the massive machine type communication (mMTC) use case has been implemented in the standard.”
mMTC is intended as an evolution of the LTE-M/NB-IoT enhancements to the 4G standard. Since NB-IoT has only just started to appear in commercial products, there is no immediate demand for a successor. Over time, fifth generation mobile networks will however become necessary to cope with the expected exponential growth of IoT connections and data traffic.
The report identifies homeland security as an area where 5G cellular IoT can have a major impact already in the early 2020s. “5G enables the deployment of high-density networks of AI-supported security cameras to monitor anything form security-classified facilities to national borders or entire cities”, says Mr. Ryberg. “How this technology is used and by whom is likely to become one of the most controversial issues in the next decade.”
May 28, 2019 • Features • Hardware • janam • Rugged devices • Varlink
Varlink’s Meet the Manufacturer event is firmly established in the field service calendar. Mark Glover attended the event, held at Leicester City Football Club, to see the latest rugged devices and meet those who play a key role at the gathering...
Varlink’s Meet the Manufacturer event is firmly established in the field service calendar. Mark Glover attended the event, held at Leicester City Football Club, to see the latest rugged devices and meet those who play a key role at the gathering...
In 2016 and against all odds Leicester City Football Club provided one of the great stories and, indeed shocks, in world sport by winning the English Premier League. When the Midlands team finally lifted the championship trophy at their home ground, The King Power Stadium in May that year, few could believe their achievement, the feat made all the more remarkable that only 18 months prior they were eyeing a potential relegation to the league below.
As a long-suffering football fan - I support West Ham - Leicester’s plight gave us smaller teams hope; that the goliaths of Manchester City and Chelsea can be overcome; that it’s not all about rich chairman and money; that fairytales do come true. You’ll have to forgive my tenuous diversion here. I’m conscious the focus of this piece is not football but on discovering the venue for Varlink’s Meet the Manufacturer (MTM) event would be the King Power Stadium - an event my editor sent me to cover - then you’ll allow me the misty-eyed opening paragraphs.
That said, in service, there is much talk of disruption and how companies should look to challenge what’s gone before in order to evolve and stay ahead and in a way, Leicester’s title winning season could be seen as the ultimate ‘disruption’ to the league’s status-quo and rigid hierarchy, and while the team haven’t joined the elite ranks of super clubs (Manchester City, Chelsea etc.) they are now firmly established as a Premier League side both financially off the pitch and with their performances on it.
Disruption meanwhile in hardware, specifically hardware in service is not as frequent, which doesn’t mean it’s not evolving; far from it. Service software providers – quite rightly - are extremely reticent in altering their hardware foundation as Mike Pullon CEO of Varlink explains. “A company that writes software for a niche, field service opportunity, whatever it is, is actually far more focused on their own business and the need to change is often driven out of necessity rather than any great desire,” he says. “When you’re writing your software, you’re enhancing your software, you’re taking care of business, you’re looking after your customers. The last thing you want to do is change the hardware platform you use.”
Mike founded Varlink in 2005. The company, a leading distributor of barcoding and data capture and EPOS products, feeds the service industry with rugged devices and hardware. Now in its 14th year, the firm’s annual MTM event serves to bridge the gap between customer and manufacturers, which today includes, among others, Zebra, Honeywell and Data Logic. Given the longevity of the event, I ask why it is so important for customers to see and experience the devices on show.
“Where do they go for their knowledge?” he asks. You go to the internet, you look at some websites and you actually find one product looks much the same as another. You don’t get a chance to feel the weight, feel the quality. It sounds really basic, but you know, until you hold one of those devices...where are the buttons positioned? How tactile is the screen? What’s the robustness? What’s the resilience? What are the charging options? So there are no UK shows that bring as many specialist, some might say niche, manufactures together.”
Mike suggests marketing emails and tweets replacing conversation between manufacturer and a specialist systems company, particularly those in niche verticals – which service tends to operate in – is missing the mark, creating a space for the event. “The communication between a hardware manufacturer and a specialist systems company, somebody providing for a particular vertical, has become stretched,” he says.
“There’s an assumption that email communications are going to carry the message about product, technology, opportunities to a customer base that’s just waiting for that communication. The last few years we’ve seen the slimming down of that conversation.”
Among the larger, big-name manufacturers such as the aforementioned Zebra, Honeywell and Datalogic and Janam Technologies. They produce operating system platforms and rugged hardware which they distribute to a reseller or software house to tailor, for example, a picking or delivery task. Robert Hurt is the firm’s EMEA General Manager and we find a quiet corner, among the beeps of demos and buzz networking, to discuss the company’s philosophy.
“Our approach is to provide people with a business tool that will work for as long as we can possibly keep it going,” he says, “and we’ll provide a service for as long as we’re able to obtain the components in order to do that. The differentiation for us is about providing a level of service.”
Compared to their consumer counterparts, rugged devices have a longer life. Failing batteries which are built in to ubiquitous Samsung and Apple smartphones are the common cause of failure and ring fence the two year turn around in buying habits. Having removable batteries in rugged devices means hardware can last a lot longer and keep the service technician active with the same device. “If you’re out on the road, you might not get to base for a couple of days,” Robert explains. “So we have removable batteries, which means you can take a spare battery and pop in this replacement battery. You can’t do it with an Apple phone and you can’t do it with a Samsung phone because it’s sealed giving it a limited life. We are still servicing and supporting devices we installed 10 years ago. They’re running simple business applications such as receiving a task and taking a signature, but it does the job.”
Janam do the vast majority of their business with re-sellers, who are a key demographic of visitors to MTM. I ask Robert how important the event is to the firm. “Every meeting, every conversation is worthwhile,” he tells me, “Everybody you meet is somehow connected to the industry, either as a supplier or as a customer or a reseller. We’ve been coming for as long as I’ve been at Janam. It’s always an interesting venue and an enjoyable thing to do.”
I shake hands with Robert, turn off my dictaphone and sip the final dregs of my coffee. Heading for the exit, I catch a glimpse of the football pitch, a bright, lush green that looks as smooth as a bowls lawn. Robert’s right. This is an interesting venue and I’m already looking forward to next year’s MTM event. For now, though, I’ll continue to believe that my team West Ham might one day perform the same miracles as Leicester and I have Varlink to thank for giving me that hope!
May 27, 2019 • Fleet Technology • News • fleet technology • fleet
TruTrac's re-designed TruLicence system enables operators to validate, monitor and control key driving licence and CPC compliance information.
The software combines driver licence verification and validity checks with tachograph and general compliance data for complete control. The dashboard includes widgets and alerts to highlight licence issues and potential at-risk drivers with areas of concern.
The firm made the announcement at this year's Commercial Vehicle Show where they also launched CPT Licence Check; the same effective and TruLinks - an API suite which gives developer access to key data, while removing the need for manual intervention or data duplication.
Commenting on the newly introduced products, TruTac’s Commercial Director, Jemma James said: “This was a great show for us and we were delighted to see so many friends – old and new – come along to see for themselves the wide range of operational and commercial benefits our latest compliance control solutions have to offer. Launching our third product in partnership with the CPT has also made it a show to remember.”
May 24, 2019 • News • Hardware • Rugged Mobile Device
Conker has agreed to the partnership to enable 42Gears to support the management of fleets of Conker devices for UK enterprises, and to refer and resell 42Gears’ unified endpoint management (UEM) software. A key driving force behind the development of this partnership is Conker’s customer base, as it discovered that they not only seek business rugged, fit-for-purpose devices, but that they also require an even greater degree of control, management and security across their devices.
James Summers, CEO and founder, Conker, says, “As a fast-growth British technology business, we’re constantly evaluating ways in which we can deliver even greater levels of business value to the market, coupled with the best possible fit-for-purpose mobile devices. This partnership with 42Gears is an important milestone in realising this goal.”
He continued, “After discussions with 42Gears, it became clear that it shared the same vision and ethos as Conker about enterprise mobility. We’re pleased to agree to this partnership, as it means that our business rugged devices are not only fit-for-purpose and adaptable to different business scenarios, but that organisations can be assured that they have total control and security of their devices.”
Kaushik Sindhu, Associate Vice President, 42Gears says, “Business-owned devices in the field are insecure and prone to misuse. Also, managing large fleets of devices have been challenging for IT admins. This partnership will serve to address these issues through easy device management, and with enterprises gaining a greater degree of control over their devices. It’s a mutually-beneficial association and we’re glad to have become a part of the Conker partner ecosystem now.”
Conker plans to expand its channel partnerships during 2019, as it seeks to further enhance its enterprise mobility offering for UK and global organisations. This complements Conker’s drive to provide its range of Android and Windows-based business rugged tablet, touch screen and mobile devices, along with its consultancy and support services.
After evaluating several providers, Conker concluded that 42Gears offered the most compelling best-of-breed technology, that enables the combination of its secure software with Conker’s secure hardware, to ensure even more productive business processes.
May 23, 2019 • News • Software and Apps
Accruent, the world’s leading provider of physical resource management solutions, announced today that it is has developed an integration between its Maintenance Connection computerized maintenance management system (CMMS) and its Meridian engineering document management (EDM) software. Using these products together, manufacturers and industrial organizations provide maintenance teams with fast, on-site access to dynamic asset documentation.
Comprehensive and accurate asset information enables maintenance teams to complete work more quickly and cost-effectively, increase asset uptime, and help assure worker safety. As margins are crucial to manufacturers, the resulting cost savings and improved output can have a magnified impact on company success.
For manufacturers, seemingly small improvements in output or maintenance cost savings can mean the difference between growth and fighting for survival. However, a growing shortage of skilled workers (71% of companies surveyed by the National Association of Manufacturers (NAM) in March 2019 indicated that attracting and retaining skilled workers is their greatest challenge) will require managers to seek other methods of assuring operational excellence. Analyst firm IDC predicts that by 2020, 80% of manufacturers will seek to place data at the center of their processes to increase speed, agility, efficiency, and innovation.
One example of placing data at the center of a process is to improve the depth and quality of information provided to maintenance teams and increasing the speed at which such information is delivered. By integrating EDM and CMMS, Accruent provides manufacturers and industrial organizations the ability to deliver on-demand engineering documentation to on-site maintenance professionals via a computer or mobile device.
Providing access to asset data while technicians are on-site:
• Reduces the time needed to complete maintenance
• Lowers the cost of completing work
• Decreases the duration of asset downtime
In addition, this combination provides better data to engineers who can update asset documentation more quickly and accurately. Perhaps most importantly, providing accurate, real-time asset documentation to maintenance personnel allows them to assure their safety while performing maintenance.
“Manufacturers are embracing digital transformation to improve operations and maximize returns. One of the key elements of digital transformation in manufacturing is breaking down data silos,” noted Kevin Permenter, Research Manager, Enterprise Applications, IDC. “Sharing information between engineering and maintenance teams is an example of how having a single source of truth can deliver benefits to multiple departments and initiatives. Manufacturers that are sharing data across these functions are opening up new avenues to improve productivity, maximize the value of their resources, and lengthen asset life.”
May 22, 2019 • News • Augmented Reality • Software and Apps
Trimble announce the launch of Trimble PULSE® Remote Expert, an augmented reality (AR) tool that improves the productivity of field service technicians by connecting them with support experts via video, audio and spatial annotations in real-time.
Trimble announce the launch of Trimble PULSE® Remote Expert, an augmented reality (AR) tool that improves the productivity of field service technicians by connecting them with support experts via video, audio and spatial annotations in real-time.
The AR tool provides remotely-located users with a shared, live view using the camera on a smart phone. Both users can add digital annotations, such as text or drawings, directly to the live view by accessing a simple menu displayed on the smartphone screen.
Digital annotations can be especially helpful when trying to communicate complex information remotely, or if either user is working in a loud environment. Trimble PULSE Remote Expert enables businesses across a range of industries, including construction, agriculture, telecommunications and utilities, to rapidly connect remote experts with technicians in the field.
It is a simple and powerful application for technicians who require real-time assistance when facing complex or unfamiliar situations, and ultimately helps to improve first-time fix rates, technician productivity and the overall customer service experience.
"Many organizations are looking for new and improved ways of connecting their field workers," said John Cameron, general manager of Trimble’s Field Service Management Division. "An ageing workforce and skill shortages are adding complexity to the service workflow and organizations are looking for innovative ways to address the challenges."
Leave a Reply