AUTHOR ARCHIVES: Mark Glover
About the Author:
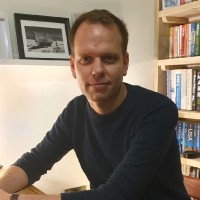
Mark is an experienced B2B editor and journalist having worked across an array of magazines and websites covering health and safety, sustainable energy and airports.
Jul 19, 2019 • News • future of field service • Berg Insight • smart meters
A research report from the IoT analyst firm Berg Insight also says smart meter penetration among electricity customers in the UK and Canada Over is projected to increase from around 60 percent in 2018 to more than 80 percent by the end of 2024.
“North America has long been at the forefront of smart grid technology adoption and a large share of the major utilities in the region are now either fully deployed or in the implementation or planning stages of full-scale rollouts. The market is however highly heterogenous in terms of penetration. Some states or provinces remain skeptical towards the business case for advanced metering investments whereas others are soon to begin a second wave of deployments”, said Levi Ostling, IoT Analyst, Berg Insight and author of the report.
Canada has reached a high penetration of smart meters through ambitious initiatives in its most populous provinces. Continued growth in North America the next few years will largely be driven by the large investor-owned utilities in the US that are yet to roll out smart meters for their customers. In addition, the large number of smaller cooperative and municipal utilities will also be playing an increasingly central role for penetration growth.
According to the report, yearly shipments of smart electricity meters in North America will grow from 8.8 million units in 2018 to 19.9 million units in 2024. Over the next few years, first-wave deployments by utilities such as Consolidated Edison, Duke Energy, Ameren, Entergy, PSEG, National Grid and Xcel Energy will boost shipments. Second wave deployments will gradually make their way into the shipment numbers at the end of the forecast period. “While increasingly powerful meters with edge intelligence capabilities coupled with advanced data analytics software will drive second wave deployments, the utilities are now also looking to leverage their existing RF mesh networks for a wider array of applications beyond metering, bringing an increasingly diverse set of devices onto their networking platforms,” concluded Mr. Ostling.
Jul 18, 2019 • News • future of field service • Ericsson • smart automation • smart factory
Ericsson have announced plans to build its first fully-automated smart factory in the US. The state-of-the-art factory will produce Advanced Antenna System* radios to boost network capacity and coverage, including rural coverage, as well as 5G radios for urban areas, both necessary for rapid 5G deployments in North America.
The new smart factory complements Ericsson’s global supply chain, which ensures the company is working close to customers through its European, Asian and American operations, securing fast and agile deliveries to meet customer requirements. This builds on Ericsson’s previously announced strategic initiative is the U.S. market. Ericsson is also fast-tracking the launch of the next-generation smart manufacturing through a modular and flexible production setup in its existing own factories in Estonia, China and Brazil.
Fredrik Jejdling, Executive Vice President and Head of Networks at Ericsson, says: “We continue to focus on working closely with our customers and supporting them in the buildout of 5G globally and in North America. With today’s announcement, we conclude months of preparations and can move into execution also in the U.S. In addition, we are digitalizing our entire global production landscape, including establishing this factory in the U.S. With 5G connectivity we’re accelerating Industry 4.0, enabling automated factories for the future.”
Location will be announced upon concluding discussions with state and local authorities. The company is committed to the factory being operational in early 2020. The smart factory will be powered by Ericsson 5G solutions tailored for the industrial environment and will also advance Ericsson’s commitment to sustainability, including registration to pursue LEED Gold Certification.
Fast and secure 5G connectivity will enable agile operations and flexible production. This will be achieved through automated warehouses, connected logistics and automated assembly, packing and product handling, and the use of autonomous carts.
The latest technology products created in the 5G factory will enable a faster rollout of commercial 5G across the region. To ensure the high quality of products, Ericsson runs its new product introduction** and early production in-house. Over time, activities to support new product introduction will also be added to the new factory operations as local competence and knowledge of 5G is built.
Ericsson plans to initially employ approximately 100 people at the facility, which will have highly automated operations, as well as a modular and flexible production setup to enable quick ramp up and rollout.
Ericsson began operations via a production partner for the first radios for the U.S. market produced at the end of 2018. The company also established a new R&D site – a software development center – in Austin, Texas. It is located close to the Austin ASIC Design Center, which opened in late 2017 and focuses on core microelectronics of 5G radio base stations.
Jul 18, 2019 • Features • Advanced Services Group • aston business school • Professor Tim Baines • Servitization • Servitization Conference
When I joined Field Service News one word appeared more frequently in my browser and in-box than any others: servitization. Its resonance was affirmed by my Editor Kris Oldland; who, during one of our early induction meetings, explained the pivotal role it plays in modern manufacturing. Three months’ on, I flew to Stockholm, and then took a two-hour car journey to Linkoping where I was to attend a conference dedicated solely to the discipline.
So, it was during a coffee break I sat down with Tim Baines, Professor of Operation Strategy at the Aston Business School and a significant player in servitization’s evolution. I was pleased to have an audience with someone who could shed some light on an area that to a layman (me) can be slightly overwhelming. We both grabbed a coffee and one of the many excellent Swedish pastries on offer before finding a quiet corner to talk.
I started off (perhaps boldly) by explaining my slight surprise that a whole three-day conference on servitization existed; that universities have whole departments dedicated to its research – many of whom were here in Sweden presenting – and that academic papers on the subject are being circulated widely. “Business researchers observe industry,” Tim said, sipping his drink. “They’re looking for phenomena, which they are trying to conceptualize and describe and test their hypothesis and understanding. They ultimately arrive at a clinical description of what that phenomena is.”
The phenomena of servitization emerged from the marketing community in the 1980s, Tim tells me, with its first research work appearing in the European Management Journal. Sandra Vandermerwe and Juan Rada’s paper Servitization of Business: Adding Value by Adding Service was published in 1988 and the former is now credited with introducing the term ‘servitization’ to represent the addition of services to enhance a manufacturer’s commercial offerings.
However, the discipline went into incubation. That was until the 2000s when Tim, along with Andy Neely from Cambridge University and Raj Roy from Cranfield niversity respectively, were awarded a research grant from the Engineering and Physical Sciences Research Council (EPSRC) to resurrect its study. “We all put a lot of effort into it,” Tim recalls. “If you look at the citations; the academic citations on servitization; look at the highest cited papers on servitization, it was really down to our collective work.”
Thanks in part to the funding, as well as the efforts of Tim and his fellow academics interest in the discipline flourished both academically and in practice. Demand for a specialist, academic event grew and eight years ago the Spring Servitization Conference was born; its eight years testament to its growth and popularity. Its first incarnation was a workshop of sorts laying out the basic principles of what the group wanted to achieve; essentially something that was crossdisciplinary within a tight-knit, specialised community.
Tim explains: “The conference is a platform for people to network, to meet each other, to share those ideas, those insights, and to learn from a few carefully chosen manufacturers how they’re seeing the world. I think what we will see in a few years’ time, we’ll have a stronger group coalescing around the key topics. Ultimately, this is a community which could very well define an
equivalent of Industry 4.0 or Industry 5.0.”
“Don’t be put-off by the word servitization... all manufacturers can gain some value through service...”
Industry 4.0 discussions were a key part of that morning’s presentations. Chairing a debate himself, Tim asked panelists if servitization was part of Industry 4.0 or vice-versa? Away from the conference hall I pushed him on his own thoughts. “Most manufacturing companies,” he said, “would associate Industry 4.0 with what’s going on inside the factory. Servitization invariably is what’s going on beyond the factory gate. In reality servitization predates industry 4.0. It will exist concurrently, and in a few years’ time will be still going on and industry 4.0 will have come and will have gone.”
Aligning with the conference’s theme, Delivering Services Growth in the Digital Era, Tim suggests firms feel more comfortable adopting servitization as digital offered a layer of security. “Digital is de-risking, enabling those more advanced services to be offered with lower risk,” he says. “It’s making it easier for manufacturers to do it.”
The other driver, Tim continued, is a broader societal shift around service consumption superseding product consumption. “If you think about servitization; it’s not a question in my mind whether companies will make more money from services or less money from services – that’s an outdated question, an outdated conversation. It’s really a case in the way that society is going. We are consuming more services where the appetite is for more sophisticated services.” Sustainability, another large societal issue is also being bearing down on the servitization sphere.
Tim is hopeful that servitization - and industry 4.0 - can ultimately negate the environmental impact of material-heavy supply chains. He referenced a presentation that morning from Cranfield University’s Tobias Benjamin Widmer, who talked about the de-materialisation of the chain; reducing the consumption of raw materials while still achieving a desired outcome.
From that, our conversation naturally turned to regulation and the influence of Government on sustainability initiatives. Firm polices around electric cars, for example, would Tim Says, have an impact on the supply chains. “If the incentives are there for electric cars, why would you have a diesel manufacturing plant? If you don’t have a diesel manufacturing plant, then your whole supply chain evaporates.”
“Here’s an interesting one,” he smiles. “The number of rotational components in a diesel engine car: about 1,500. In an electric car: about 22. Now what’s that going to do your material supply chain?”
We finish our drinks, aware of the slow movement of delegates at they file back into the conference room, themselves refreshed by caffeine and pastries. I shake hands with Tim and thank him for his time, and we both agree to keep in touch.
The next day, I send Tim an email asking if he could possibly spare a copy of his book he wrote with Howard Lightfoot, Made to Serve. The book is seen as an excellent primer into servitization, and I said as much Tim in my email; how it could enhance my learning on a topic that I was beginning to find rather intriguing.
The book arrived in my mailbox a few days’ later; a good-looking tome with a striking cover. A contemporary, simple image of three factories, the middle one with a striking red path leaving its front gate; fanning in perspective to the base of the cover. I read the book’s preface: “Don’t be put-off by the strange word of servitization,” part of it said, “all manufacturers can gain some value through service.”
I recalled the interview in Sweden, when Tim told me about the early days of servitization; when people queried the term, wondering how you spell it, asking if they would make money out of these advanced services. “Now, we don’t have these questions anymore,” Tim had said.
What is a relatively young area of research, servitization now seems to be an integral cog of a manufacturer’s approach to revenue. As Tim suggested, technology will evolve and eventually become exctinct (Industry 4.0, for example), but servitization, as a theory and practice, will continue to grow alongside and compliment manufacturing. In short, making money from selling spare parts is no longer the revenue stream it once was.
Jul 17, 2019 • Management • News • Comarch
Is your organization’s field service management up to the mark? What if you could find a way to optimize operations so that you simultaneously improve your company’s indicators and customer satisfaction ratings?
Is your organization’s field service management up to the mark? What if you could find a way to optimize operations so that you simultaneously improve your company’s indicators and customer satisfaction ratings?
Comarch’s new e-book goes much further than that, highlighting 50 areas to be optimized in field service delivery. What’s more, it’s free to download now – one click and you can begin reading in moments.
The challenges facing companies operating on today’s field service management market demand a new approach to delivery. Environments are changing quickly, customers expect rapid issue resolution, and workforces must be increasingly agile and connected. The only realistic way to face these challenges is through automation, made possible with a comprehensive, advanced and highly customizable product.. As in every business operation, knowledge is the route to success. That’s why Comarch has produced the e-book, entitled “50 Ways to Automate Field Service Delivery”, to put the information that you need directly into your hands.
This 23-page guide prepared by field service management experts breaks down areas in which you can start to make improvements, regardless of how big or small your organization is, and no matter whether you are operating globally or on a local market. Download your copy for inspiration about the best ways to unlock the service automation potential in your company in areas such as resource management, service request management, planning and scheduling, business management, work order execution, communication and asset management.
While it may seem at first glance that 50 areas to be optimized in field service delivery is a lot to take in, the paper has made it more digestible by breaking the e-book down into the sections outlined above. The result is a handy, go-to guide that will provide food for thought about immediate and long-term strategic steps you can take; in short, you can start to maximize the benefits of your reading right away.
If you’re still not convinced that your field service management processes need automation and optimization, don’t just take our word for it. Our e-book includes data showing how one international client smashed SLA targets following FSM implementation. To find out how they did it, and even join them, download your free copy of “50 Ways to Automate Field Service Delivery” now.
Jul 17, 2019 • Fleet Technology • News • fleet • lastmile • BT • Parts Pricing and Logistics
The first BT Field Engineering Forum, sponsored by Kuehne+Nagel and held at London's BT Tower on 17 June, covered a wide range of topics on how the sector can move forward.
The host, BBC newsreader Huw Edwards, brought together industry experts to discuss the rapid evolution of technology and how innovations such as self-driving cars, drones, blockchain – and even BT’s own Final Mile solution – can help organisations to improve performance and efficiency.
A key theme was customer service and how the supply chain is responding to a significant shift towards an environment where the customer is central. Keynote speaker and author Sean Culey explored the disruptive technological models that are driving this change, and what businesses must do to deliver the experience that customers now demand.
Throughout the day, speakers and panellists demonstrated the impact of change upon major market sectors such as retail, or specific organisations such as the NHS and the Ministry of Defence.
Crucially, each speaker had practical, proven solutions to these challenges, which they shared with over 100 delegates from across the UK supply chain.
Topics ranged from perceptive fulfilment – using data to pre-empt customer buying decisions – or the use of personalised procurement portals for faster, more efficient operations.
The event also gave BT the chance to demonstrate the power of its Final Mile solution for field engineers. Final Mile is a nationwide network of secure lockers and boxes, used as intermediary stock locations by organisations with large field engineering teams. By storing parts at strategic sites along engineers’ routes, businesses can reduce driving hours to serve customers faster, remove cost and minimise environmental impact.
Stephen Maddison, Managing Director of Final Mile, explained why the Field Engineering Forum was so important. “Not so long ago, organisations only reviewed their supply chain every three years or so," he said. Today, given the pace of change and the exciting new technologies available, businesses need to keep their finger on the pulse continuously.That’s why we created the Field Engineering Forum – a place where industry leaders can tackle these issues head-on, share best practice and forge new partnerships. The supply chain is the bloodstream of the economy, so it’s vital it’s in a healthy state. We’re delighted with the quality of debate and are looking to repeat this event next year.”
Jul 17, 2019 • Features • Augmented Reality • Future of FIeld Service • Workforce • IFS • skills • The Big Discussion • OverIT • Librestream
In the first of a new four part series, we turn our attention to Augmented Reality where our panel includes Stephen Jeffs-Watts, Senior Advisor Service Management, IFS, Francesco Benvenuto Product Marketing Manager, SPACE1 by OverIT and John Bishop, President, Librestream...
Why should field service companies deploy an augmented reality solution if they already have a peer-to-peer video tool (such as Facetime or Skype) already available and free to use?
JOHN BISHOP, PRESIDENT, LIBRESTREAM
Choosing a video chat product as a remote expert augmented reality (AR) solution can seem like an easy path to fulfilling an immediate need.
As AR platforms and capabilities like remote expert guidance have matured, enterprises have developed clear requirements for security, IT controls, usability and performance. Requirements that these kinds of tools are not able to meet. For example, how will the solution perform in low bandwidth environments? Can IT control how much bandwidth will be consumed?
How can I quickly engage supply chain experts and customers? How can I be sure my content is safe and meets privacy requirements?
We deployed the first AR remote expert solution in 2006 – long before remote expert guidance was part of AR. Over the past 12+ years, our enterprise customers like Rolls Royce, NOV, Colgate-Palmolive, SGS, and hundreds more have guided the development of our solution to solve these difficult challenges.
FRANCESCO BENVENUTO, PRODUCT MARKETING MANAGER, SPACE1 BY OVERIT
Augmented Reality does not imply the use of a mere Remote Support solution but of an advanced tool aiming at supporting field technicians in their daily tasks through advanced collaboration and content sharing features.
AR solutions, such as OverIT’s product SPACE1, offer both real-time remote assistance and access to pre-built AR work instructions simultaneously.
In this way, support means collaboration and remote problem solving, but with a groundbreaking concept in mind. When assistance was guided by standard videos, both field technician and remote operator had to rely solely on voice instructions. SPACE1 is one step ahead, allowing experts to make marks that stick where drawn and annotations to be displayed on the users’ point of view while supporting them. Moreover, it enables the sharing of digital twins to be set where the remote expertise is needed, thus broadening traditional field working modalities and creating a brand-new cooperative virtual environment. See it in action here.
By using AR products users can capture images, record live support sessions to retain and share the expert assistance (both verbal and supported by visual annotations) in the future or even generate reports and offer actionable insights into improvement opportunities while providing additional employee training.v
STEPHEN JEFFS-WATTS, PRODUCT MANAGER, SERVICE MANAGEMENT, IFS
AR is a far broader topic, with wider use-cases and implications than simply being used for video calls and ad-hoc collaboration.
One of the most compelling use-cases is in service call avoidance; where AR, when implemented in a seamless manner, empowers contact agents with enhanced diagnostics capabilities and tooling – being able to see and remotely guide the customer in triage with directive instructions, document sharing and image mark-up. These capabilities can reduce down-time, avoid the need to send a field technician to site and thus directly improve customer satisfaction. Additionally, compliance obligations can also be met through integrated session recording; which isn’t possible in the peer-to-peer space.
That same capability can then be deployed in the field; giving the technicians and the remote experts guiding them much wider capability with a resulting increase in effectiveness and efficiency. In this way, the technology increases first-time-fix rates, improving cost-to-serve and providing another dimension in improving the customer experience.
The second part of the big discussion will be published next week, when the panel answer questions on the role that AR can play in the challenges that come with an ageing workforce.
Jul 16, 2019 • News • apps • health and safety • News Software and Apps • Software and Apps
Celtic Technologies now use StaySafe to provide better protection for their field workers when working underground or remotely.
Celtic Technologies now use StaySafe to provide better protection for their field workers when working underground or remotely.
StaySafe is an app and surrounding cloud-based monitoring service which tracks a lone worker’s location via GPS and alerts their manager if an employee triggers an alert or they do not check-in within a specified time.
Celtic Technologies provide integrated environmental services which operate in the UK, France,the USA and Canada. They are a contaminated land remediation contractor specialising in ground and groundwater treatment, materials management, asbestos management, and brownfield improvement.
Prior to StaySafe, the company relied on traditional safety practices such as asking staff to send text messages or call in to let management know of their whereabouts. However, this method relied heavily on employees remembering to contact the office and was also problematic for those that carried out work in remote areas.
Stephen Kidley Senior Operations Manager at Celtic comments “Set up of the app was very quick and we were all impressed with its simplicity. Our staff are really pleased with the app and feel much more comfortable knowing that they have it with them. The customer service we have received from StaySafe has been excellent and the solutions they provide are great value for money”.
Don Cameron CEO at StaySafe adds “It can be a huge challenge to manage and maintain the safety of field service workers due to the dangerous environments they’re constantly exposed to, StaySafe helps to keep these vulnerable employees safe by offering an innovative and simple way to monitor their safety”.
Jul 16, 2019 • Features • Management • health and safety • tablets • Rugged Mobile Device
Digital devices have over the years become more portable. For service technicians this improvement in usability has undoubtedly improved the way in which they work. However, the industry’s swift adoption of these devices has perhaps been too rapid, meaning health and safety guidance is yet to catch-up with the potential ergonomic risks that smartphone and tablet use carries.
I’ve written articles in these pages (and in our recent edition of The Handy Little Book) on health and safety, referencing the potential impact on a lone worker’s wellbeing, given that their work is carried out mostly in isolation. However, another area of the broad H&S spectrum that lone workers or field service engineers are vulnerable too is musculo-skeletal dis-orders (MSDs).
Defined by the UK Health and Safety Executive (HSE) as “any injury, damage or dis-order of the joints or other tissues in the upper/lower limbs or the back", MSDs, according to a study carried out by HSE for the period 2017/2018, shows 469,000 workers are suffering with cases of work-related MSDs, which includes long and short-term conditions. The knock-on result on productivity is 6.6 million working days lost as a result of the condition, the same research reveals.
The study does not uncover the extent to which lone or mobile workers suffer, although the top three industries where workers are most affected include fishing, forestry, agriculture (grouped together), construction and then transportation and storage (also grouped) will arguably include a section of field-based lone workers. The condition is also common for office-based workers who are vulnerable to neck or back issues, brought on by incorrect posture while using computer equipment at a desk.
It shouldn’t be ignored however, that while field service engineers are desk-free, incorrect ergonomic use of tablets and phones – the tool of the trade for most lone workers – carries its own ergonomic risk.
But with rugged tablet and laptop devices now a ubiquitous part of an engineer’s kit why hasn’t there been more attention on their dangers? It’s useful to look more generally at society’s relationship with smartphones and tablets, which are now commonplace in people’s lives.
It is estimated that five billion people in the world own a mobile device, of which, half of these are smartphones. Indeed, the rate at which we’ve adopted them is staggering which is primarily down to their relative ease of use and in-turn part of the reason why they have found their way into engineers and technicians hands who require rugged devices that perform but also offer a practicality. However, it’s this natural uptake both in public and the workplace that, according to one expert, is enabling risks around their ergonomic use to go unnoticed.
Ed Milnes is Founder and Director of Guildford Ergonomics a consultancy firm in the UK that specialises in ergonomics and human factors in the workplace and has contributed guidance and research into the risks of smartphone and tablet use.
“I think there’s a psychological element to it,” he tells me over Skype. “It’s as if it hasn’t come onto people’s radars because we use these devices so much in our everyday lives anyway. We accept them as something that – because they’re always around – they must be safe that there can’t be any inherent risks with them. When you use them day in and day out, almost every day, it does become more of an issue.”
"It is estimated that five billion people in the world own a mobile device..."
MSD risks are linked to exposure and how long how and how often is spent on activities. In the case of service engineers this does oscilate in line with the complexity and length of a job but as technology advances – with AR soon to play a major role – then engineers will be looking at their tablets and then moving their vision and neck towards the asset and then back to the tablet.
It will, inevitably, place stress on the back and shoulder and other areas.
However, it’s the neck region, Ed tells me, that is most vulnerable to pain when using these types of devices. “The one area that does stand out, where we’re clear that there is an issue is in the neck area and the development of neck pain,” he says. “This is the absolute number one area when it comes to these devices.”
He acknowledges though, given the nature of lone workers, it is difficult to collaborate and collect insightful data. “A lot of the data on discomfort is basically self-reported data, so it’s very subjective. For example, how long people are using the devices for and how often they’re using them. It’s based on people estimating how long they’ve spent on them and very often you get people underestimating.”
Research ambiguity can in part be attributed to the lack of guidance that exists on the topic. HSE who inform legislation around health and safety in the UK, seem to have been caught napping when it comes to specific guidance on smartphone and tablet use. Their L26 guidance document, which advises on Display Screen Equipment was published in 1992 and updated in 1998 but fails to incorporate the mobility trend. “It [the L26] did its best to anticipate the development of things,” Ed sympathises, “but there is no official formal kind of guidance. It’s a real difficulty because you not only have that lack of regulatory clout behind doing anything. But it’s also about the physical aspect. People by the very nature of the work they are doing, are out and about, so they’re not under anyone’s eye.”
Back then to those office workers who receive regular risk-assessments around their display screen equipment (computer, chair etc.). For their mobile colleagues it’s perhaps unreasonable to expect a health and safety manager to attend each engineer’s call-out to ensure they are using a tablet correctly.
Ed does suggest however that companies and management need to incorporate more of a broad-based assessment and take more of an active role in the process, particularly around training, acknowledging the type of work they conduct. “It’s also about the physical aspect,” he explains. “People by the very nature of the work they are doing, are out and about, so they’re not under anyone’s eye. There has to be an understanding on the part of the company, including the health and safety manager who can potentially envisage the workers are going to face and put controls in place; putting devices in place that they can refer to to help them use their own mobile devices more safely.”
“The big thing really is training,” he continues, “which I know is right down the bottom of the hierarchy of control, but ultimately, it’s what you’re left with when everything else doesn’t really stack up as a solution.”
As devices continue to evolve more emphasis will need to be placed on their correct handling. A solution is undoubtedly required which should be driven by concrete guidance.
For now though, employers need to recognise the ergonomic risks associated with the hardware as continued incorrect use could spell greater difficulties for workers’ health later on.
Jul 15, 2019 • News • connected devices • smart automation • Software and Apps • Industry 4.0
Former Google Enterprise sales leader, Nathan Radar, will drive client acquisition strategy to the next level, connected worker platform firms says.
Former Google Enterprise sales leader, Nathan Radar, will drive client acquisition strategy to the next level, connected worker platform firms says.
As CRO, Rader will spearhead the company's revenue generation and customer expansion strategies, driving deeper collaboration among teams across the company and its partner ecosystem to ensure alignment on all go-to-market initiatives.
Rader joins Parsable with over a decade of sales experience at Google Enterprise, most recently as head of sales for Google Cloud. As one of Google Cloud's first enterprise sales leaders, he more than doubled revenue and significantly grew a highly cross-functional sales team. Prior to Google, Rader helped launch Oracle's Fusion Middleware technology group, overseeing triple digit growth. He began his sales career at IBM as a client sales manager focused on emerging businesses.
"This is a major coup and milestone for the company. Nathan has an impressive track record of success in enterprise software sales as well as an admirable leadership style that is precisely what Parsable needs at this pivotal moment of growth," said Lawrence Whittle, Parsable CEO. "As the connected worker category continues to mature and as every industrial company in the world recognizes the value of digitally empowering its frontline workers, we have an incredible opportunity to increase market share. We're thrilled to have Nathan on our executive team and expect him to play an important role in our expansion."
Rader said: "Industrial companies are facing pressure to address high-priority operational challenges and improve execution of key frontline business processes. I've been in technology for 20 years, and it's rare to find a robust platform like Parsable that can be deployed quickly and show quick time to value. The flexibility of the platform is a game-changer in the industrial world, and I'm excited to be a part of the digital transformation taking place inside industrial workforces."
Leave a Reply