New working relationship for BT Fleet Solutions and Winton Engineering announced at Commercial Vehicle Show...
AUTHOR ARCHIVES: Mark Glover
About the Author:
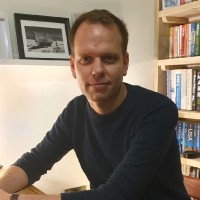
Mark is an experienced B2B editor and journalist having worked across an array of magazines and websites covering health and safety, sustainable energy and airports.
Jul 09, 2019 • Fleet Technology • fleet • fleet management • Fleet Operations
New working relationship for BT Fleet Solutions and Winton Engineering announced at Commercial Vehicle Show...
In a move to enhance the benefits both businesses can provide to customers, BT Fleet Solutions and Winton Engineering have agreed a new working relationship to provide maintenance and servicing on Winton Engineering systems using BT Fleet Solutions’ network of garages and mobile engineers.
The contract will allow BT Fleet Solutions to better service both internal and external customers’ vehicles with on-vehicle power systems. Having worked together through mutual customers since 2006, this relationship is the logical next step for the businesses who are both highly-respected suppliers in the UK utility sector.
Simon Ungless, business development director at BT Fleet Solutions, said: “Winton Engineering’s systems are used by many BT Fleet Solutions utility customers, so the additional services we will now provide will serve to further strengthen our product offering and relationships with these customers.”.
For Winton Engineering’s existing customers this will provide increased coverage for maintenance and servicing of the Winton on-vehicle power systems. It will also provide them with a greater flexibility for systems to be serviced either on site using one of BT Fleet Solutions’ mobile engineers, or at one of BT’s 65 garage locations, reducing the time and fuel required by customers to reach their nearest available site.
Winton customers using BT Fleet Solutions will also have the added benefit of being able to get their vehicles serviced at the same time in addition to servicing the Winton systems, a significant potential reduction in VOR (vehicle off road) time.
Andy Jones, managing director at Winton Engineering, commented, “BT Fleet Solutions is a respected name in the UK utility market and so working with them matches nicely with the positive reputation that the Winton on-vehicle power systems have for robustness, reliability and efficiency.”
Jul 09, 2019 • Features • Management • servicemax • Software and Apps • Customer Satisfaction and Expectations
It’s been an eventful 12 months for ServiceMax. In April, Scott Berg relinquished his CEO position making way for IPC System’s Neil Barua. In December, parent company General Electric sold their majority stake (held since 2017) followed by SeviceMax’s own acquisition of real time communications outfit Zinc.
It all meant that the Maximize Bologna, an event consisting of a day of presentations from company figures and client case studies - and the first of four events in 2019 taking in London, Chicago and Tokyo - would represent something of a re-set for ServiceMax, an opportunity perhaps to usher in a new era.
With all this in mind, these are the five key threads I picked-up while in Italy:
1. Service Execution Management
Lubor Ptacek, the company’s SVP of Product and Solution Marketing, gave the first major presentation of the day, and following a brief run-through the firm’s 19-year history including their start-up origins to the role GE played in their development, he forecast where the sector is headed, aligning changes in the industry to ServiceMax’s new software category Service Execution Management, a new type of approach that includes field service and asset service management respectively.
2. Platform Is Now Managing 200 Million Assets
In the same presentation, Ptacek revealed a significant landmark in the firm’s growth, telling delegates that ServiceMax’s cloud-based platform is currently managing 200,000,000 assets. It’s an extraordinary statistic affirming the company’s core-service goals are statistically being met.
3. Real-Time Communication Will Play A Key Role
The firm’s integration of Zinc’s mobile-based app as a module into its own software platform signals their commitment to real-time communication in the service journey. Text, voice, video, handsfree, push-to-talk and broadcast features will all be possible on the mobile-first solution which encourages interaction across groups to share issues and offer knowledge. “The perfect combination of Zinc’s modern, real-time communication with ServiceMax’s cutting edge and comprehensive suite will be unparalleled in the market,” Zinc President, Stacey Epstein said at the time of the acquisition affirming the strategy.
4. Automation And Anxiety
“Competencies are by far the main obstacle according to companies undertaking a path to industry 4.0,” Nicola Saccani, Associate Professor at Brescia University told audience members during his presentation. Professor Saccani, a specialist in service and digital transformation, suggested that employers are struggling to keep up with the pace of which technology is progressing. This, along with the growing competency gap created from retiring engineers and new blood coming in, presents one of the biggest challenges to the sector.
5. An Excellent Keynote
Maximise events always draw a special keynote speaker and this year was no exception with Fausto Gressini, the world’s most successful MOTO GP and MOTO GP manager in superbike history sharing his thoughts on the evolution of his sport.
Superbikes, Gressini explained, have become data sponges.
They absorb reams of information from its tyres and engines, from its brakes and exhaust; an endless spout of data that needs to be interpreted to the team’s advantage. Furthermore, the rider, as well as navigating bends at a hair raising 140mph, is expected to understand the information coming through and relay any trends back to his mechanics.
It was an excellent keynote and entirely relevant. On the surface a field engineer and superbike rider may not have a huge amount in common but when it comes to data collecting and refining there is a definitive link. It was a fascinating session and one that delegates appreciated and could genuinely use in their own processes going forward.
A Final Thought
ServiceMax is in a transition period, albeit a positive one and the event nodded towards another interesting 12 months. We’ll be following their progress in these pages as well as fieldservicenews.com. Stay tuned!
The next ServiceMax Maximise event takes place 7 to 8 October in London. Click here for more information.
Jul 08, 2019 • Features • Management • Future of field servcice • Field Service Management Solutions • localz • Mira • Augmentir
From Singapore to Sweden and from California to Coventry and everywhere in between - where there has been an opportunity to learn more about developments in field service we’ve been there. As such we’ve spoken to more field service management professionals and field service solution providers than anyone else on the planet and we think we’ve a pretty good idea of what the solutions the industry is most keen to see and the companies that have emerged to deliver the solutions that meet those needs.
So without further a do here is our list of three of the best new solution providers service the Field Service Sector who have really impressed us across the last 12 months...
Localz
You can’t go to a conference, not just in field service, but in any sector and avoid the term Uberization. Within our sector alone there has been endless articles, white papers and presentations on how to ‘Uberize’ field service. Half of these are just focused on what the hell Uberization means in the first place.
Well a good place to start is implementing Localz, which can act like a plug in to go on top of whichever flavour of FSM or scheduling tool you have and deliver a very cool end customer interface that allows them to see the ETA of your engineer on route across the last mile.
Localz is capable of a ton of other stuff all centred around ‘Last Mile Communications’ but this really is the Uberization of Field Service many have called out for and with an implementation of weeks it is little wonder the have already secured some very high profile clients like British utilities giant British Gas. Localz can be as lightweight as a plug-in and delivers exactly what the market has been asking for in a brilliant way.
Mira
When Google Glass first came around everyone in the field service sector rushed to embrace it. All the Field Service Management Software guys raced to get the first App developed for it and there were loads of reports of companies doing beta trials everywhere.
Why? Because Hands Free working in field service just makes a massive ton of sense.
However, ultimately as we know the idea was great the technology not so much. And whilst there have been some very good alternatives coming onto the market in the field service sector for a while now, nothing has dominated because the price point for entry is just so high companies are uncertain if they will see a quick ROI if any at all.
Enter Mira who have the potential to absolutely dominate in the sector through a simple, well thought out and smartly designed headset that takes advantage of the fact that pretty much every engineer has a phone in their pocket.
Their headset allows a phone to be placed into the frame, much like the gaming VR headsets such as Samsung’s Gear VR or Google’s Daydream but also gives the user visibility of the real world through a clear display.
The headset itself is exceptionally well thought out and you can see the team behind this product come from a design background - little touches like easily attaching to standardised hard hats for PPE compliance are testament to this. Similarly, as the headset is literally powered by your engineers existing smartphone there is no additional MDM concerns. A low cost, yet effective way to implement AR today.
Augmentir
Sticking with Augmented Reality, the last company on the list is Augmentir, who come with a very strong pedigree and a very neat approach to things.
At first glance, you may be forgiven for thinking that Augmentir are just another of the many Augmented Reality providers that have suddenly noticed the potential in the field service market. However, scratch the service and you will see that there is actually quite a lot more to them than that.
The first thing to pay attention to is who is behind this brand. It is the same team that previously developed ThingWorx, which was ultimately sold to PTC and became the backbone of their IoT solution and recognised as an industry leading solution. They were also responsible for Wonderware which statistically almost two-thirds of our readers from the manufacturing sector will already be using. So when these guys rend to turn their hands to something they have a pretty good track record of getting it right.
However, the really interesting thing about Augmentir is that they’ve gone far beyond the initial approach that many of their peers are offering when it comes to Augmented Reality (AR) and dived straight into an Artificial Intelligence (AI) powered approach. In their own words they position themselves as ‘the first software platform built on Artificial Intelligence in the world of the augmented or connected worker.’
This could be a significant game changer in terms of AR being used in field service because it takes the technology beyond its initial use case and into something far, far more useful by leveraging another exciting technology in AI directly alongside it. In fact, as their VP Marketing Chris Kuntz told us they are “a 100% AI first company” who have just been smart enough to realise that AR is the interface that makes most sense for modern field service operations.
Jul 08, 2019 • Features • Parcel Holders • Parts Pricing and Logistics
Ed Fraser, Managing Director at Parcel Holders responds to a Field Service News article on spare parts being the "black sheep" of the sector and wonders what role the supply chain will play in parts logistics...
Ed Fraser, Managing Director at Parcel Holders responds to a Field Service News article on spare parts being the "black sheep" of the sector and wonders what role the supply chain will play in parts logistics...
Following on from Kris Oldland's informed piece about parts management labelled the ‘black sheep’ of the service industry, I’d like to reflect on this constantly shifting sector of the service industry, discuss what’s available (and most often used), and offer some solutions.
As MD of a company which was set up to solve problems associated with getting parts to engineers, I can sympathise with the issues faced by parts managers - there are just so many ways to manage parts, and to get them where they need to be. Maybe you’ve just got to grips with one method when your engineers or boss start suggesting something else entirely! We know it can take a while for us mere humans to catch up with today’s constant change in technological innovation.
Let’s face it, technology has made much of the world and how we interact with it, almost unrecognisable to that of 20, even ten years ago. Some of us even remember flicking on a light switch to activate the tungsten element in a spherical bulb! Halogen bulbs, mini fluorescent tubes, long-lasting energy efficient LEDs… now, if we have Alexa, we don’t even need to lift a finger to illuminate a room. The way we socialise, watch TV, drink coffee, light, heat and cool our spaces, and pay for it all, presents us with a vast arena of change and choice.
But is change just due to technological innovation? Well, I would argue it has just as much to do with development in laws surrounding regulation.
Remember those dirty words: CFC gases? Those ozone-depleting nasties? Well, happily of course, they’ve been replaced with more enviro-friendly refrigerant gas. Renewables: wood pellet heaters, solar-electric systems, ground source and air source heat pumps are increasing in popularity. Your client wants the latest ‘green’ thing, it makes them look and feel good. But are your engineers up to installing, maintaining and fixing it? That’s the real challenge, getting the parts to them to do these jobs shouldn’t be.
Now, if your answer to improving service is to increase van stock, then you may have missed the point slightly. Sure, if you’re completely virtually integrated and your engineers are employed to fix one specific brand of machine, then van stock may make a lot of sense. But, for companies looking to win new business where part of the deal is maintaining a portfolio of equipment from a broad and expanding range of manufacturers, then van stock can easily become obsolete. It’s a burden on your service rather than an asset.
It's worth asking whether metrics show if doubling the van stock you can confidently predict doubling first time fix rates. If the answer is no, then this would indicate increasing vanstock is putting your business on a path to Malthus’s l law of diminishing returns. And with continual change in the marketplace, this method of managing parts is only going to get harder and more costly. Nonetheless, common sense will tell us there are certain things that the field tech shouldn’t turn up to a job without. But the more we stock the more we are depending on knowing the future and the further we get from the ‘just in time’ work philosophy which is considered a large factor in the meteoric growth of Japan’s economy.
I would argue that the way forward is better phone diagnosis and a faster supply chain. Sourcing parts and negotiating terms with suppliers can be a profession in itself! But if you want to keep this in-house then perhaps parts managers should spend their time sourcing supplies that can meet your business demand rather than stocking up on ‘general’ components that are increasingly unlikely to be needed.
"I would argue that the way forward is better phone diagnosis and a faster supply chain..."
In light of this, many field service businesses are looking to pass back their stock of inventory to primary suppliers. But what they may not realise is that these suppliers are equally reticent to order smaller and smaller batches of parts they may never ship. As such, suppliers are increasingly drop-shipping parts direct, and in doing so, not just saving themselves the threat of investing in static inventory but also saving on the extra logistics of the part travelling to their warehouses, plus the time it takes to stock the inventory only to subsequently pick and package the part once again for re-shipment.
It looks like this trend inevitably leads to more and more complex supply chains that are increasingly hard to manage. All of which makes the ‘holy grail’ of first time fixes ever more elusive.
In addition, sourcing the right part is a very different ball game to getting it into the hands of the engineer that needs it. Most field service businesses make all their revenue charging for the parts and service their engineers provide to their clients. But I’d argue that product complexity and increases in regulation mean that the scope of equipment an engineer could have at one time ‘tried their hand at’, has become ever more restricted. This, together with the natural desire to win new business means engineers increasingly work over wider territories. If you’re going to have them return to base to collect parts then during that time on the road, their skills (which you’re paying for) are redundant as they assume the work of expensive same day couriers.
OK, so I’ve thrown out stocked vans and driving to base/depots. What now?
If parts managers want engineers generating income, then they don’t want them sitting at home waiting for parts to be delivered. Sending parts direct to clients sites? It works in some sectors, but the bigger the site, the more this tends to be fraught with problems as parts are mislaid and jobs are delayed, as recipients on front desks fail to report parts’ arrivals. (This method is impractical of course in the domestic market with homes empty during working hours.)
Logistics businesses have seized the opportunity to offer premium solutions for the field service sectors with in-night delivery, forward stocking locations and locker boxes. But, far from simplifying the delivery process, they invariably require the part to travel though their delivery network, protracting an ever lengthening supply chain.
So, what if the supply chain could be turned on its head? What if we take inventory management out of the equation altogether? This at least seems to be making life easier for parts managers. Some are now cutting out the parts journey from supplier to van / home / site / locker box. Instead they are sending parts direct from suppliers and their suppliers, straight to engineers using alternative methods like PUDOs (pick up, drop off points) which are ‘open all hours’ and in convenient locations, within a few miles of engineers’ homes.
Field Service business can rest assured, innovations and change isn’t restricted to physical products. It’s equally providing greater insight into the supply chain than ever previously achieved and minimising the path and time taken for engineers to receive the parts they need. But perhaps in the midst of technological advancement and future-gazing, we may just need the human touch more than ever.
Click here for more information about PUDOs.
Jul 08, 2019 • News • 5G • future of field service • research report • Ericsson
Ericsson has released a new ConsumerLab report - 5G Consumer Potential - which busts industry myths surrounding the value of 5G for consumers and outlines the opportunities available for communications service providers.
Ericsson has released a new ConsumerLab report - 5G Consumer Potential - which busts industry myths surrounding the value of 5G for consumers and outlines the opportunities available for communications service providers.
1. 5G offers consumers no short-term benefits.
2. There are no real use cases for 5G, nor is there a price premium on 5G.
3. Smartphones will be the “silver bullet” for 5G: the magical single solution to delivering fifth-generation services.
4. Current usage patterns can be used to predict future 5G demand.
The key findings of the study include the fact that consumers expect 5G to provide relief from urban network congestion in the near term – especially in megacities, where six in 10 smartphone users report facing network issues in crowded areas. The respondents also anticipate more home broadband choices to be available with the launch of 5G.
Another key finding is that current 4G usage patterns are not indicative of future usage behaviors. Video consumption is set to rise with 5G. Consumers expect to not only stream video in higher resolutions but also use immersive video formats such as Augmented reality (AR) and Virtual reality (VR), resulting in an additional three hours of video content being watched weekly on mobile devices by users in the 5G future when they are out and about, including one hour wearing AR glasses or VR headsets. The study also reveals that one in five smartphone users’ data usage could reach more than 200GB per month on a 5G device by 2025.
Jasmeet Singh Sethi, Head of ConsumerLab, Ericsson Research, says: “Through our research, we have busted four myths about consumers’ views on 5G and answered questions such as whether 5G features will require new types of devices, or whether smartphones will be the silver bullet for 5G. Consumers clearly state that they think smartphones are unlikely to be the sole solution for 5G.”
This latest Ericsson ConsumerLab study is based on 35,000 interviews with smartphone users aged 15 to 69, carried out in 22 different countries. The views of the participants are representative of almost 1 billion people. To gain a perspective on industry sentiment regarding the consumer value of 5G, a further 22 interviews were conducted with experts including academics as well as senior executives working for telecom operators, handset and chip manufacturers, start-ups and think tanks.
Jul 05, 2019 • Fleet Technology • News • paragon • paragon routing • fleet • fleet management
Paragon has enhanced its routing and scheduling software with the introduction of resource management functionality to help fleet managers better manage utilisation of all available drivers.
Paragon has enhanced its routing and scheduling software with the introduction of resource management functionality to help fleet managers better manage utilisation of all available drivers.
The new functionality allows fleet operators to track drivers’ holidays, shift patterns and hours worked, automatically factoring all of this in to transport plans. With the driver shortage problem continuing to challenge transport operations, enhanced resource management is vital for fleets of all sizes.
Driver availability is just one of hundreds of parameters that a planner has to juggle when creating transport plans. Planners are under pressure to take account of individual driver preferences such as shift times, break times and overnight assignments, all the while aiming for maximum efficiency across the transport operation. The new resource management functionality from Paragon will allow fleet managers to:
- Manage holiday entitlement and approval to avoid too many drivers being away at the same time;
- Automatically generate advanced shift schedules to provide forward visibility and control;
- Comply with working time limits at an individual driver level;
- Track individual driver hours accumulated to avoid overtime.
Planners can now ensure delivery routes are efficient and make the best use of drivers and vehicles while factoring in drivers’ preferences. Furthermore, the planning process itself becomes more efficient. Planners can automatically allocate available drivers to a plan, removing the need for the transport office to spend time allocating drivers to routes. Total visibility of all drivers’ availability, captured in a single system that feeds in to the planning process, brings a reduction in planning time and eliminates the risk of human error. This represents a significant improvement over using paper-based or multiple software systems.
Building on the required skills functionality which is available as standard in Paragon’s routing and scheduling, fleet managers are also able to create their own list of driver skills such as qualified gas fitter or carpenter and the appropriate tools required for each job. Paragon’s routing software will then ensure that calls are only allocated to appropriately skilled drivers and that skilled resource is allocated appropriately.
“Our new resource management functionality allows fleet managers and planners to do more with less. At Paragon, we invest about a third of our turnover in research and development every year helping customers develop a continuous improvement process that solves real-world, everyday transport problems,” said William Salter, Managing Director of Paragon Software Systems. “With resource management functionality, you gain peace of mind that you are achieving maximum efficiency from all your available assets, including drivers.”
Jul 04, 2019 • Future Technology • News • future of field service • manufacturing • cloud • IoT
Manufacturers will more than double Multicloud use in the next two years, a new report predicts.
Manufacturers will more than double Multicloud use in the next two years, a new report predicts.
Nutanix has announced the findings of its Enterprise Cloud Index results report for the manufacturing sector, measuring manufacturing companies’ plans for adopting private, public and hybrid clouds.
The report revealed that the manufacturing industry’s hybrid cloud usage and plans outpace the global average across industries. The deployment of hybrid clouds in manufacturing and production companies has currently reached 19% penetration, slightly ahead of the global average. Moreover, manufacturers plan to more than double their hybrid cloud deployments to 45% penetration in two years; outpacing the global average by 4 percent.
The manufacturing industry is at an “innovation impasse,” 1 meaning manufacturers have a desire to innovate and drive transformation, but legacy IT systems have the potential to constrain their ability to do so. The opportunity for manufacturers to embrace digitization efforts including “Industry 4.0” initiatives can break the impasse, but executives must focus on new opportunities to create value and not only prioritize traditional business operations. Manufacturing organizations face the constant challenge of trade-offs: they are under pressure to meet current productivity and operational goals in an increasingly global and highly competitive marketplace, but they also need to invest in future growth.
This challenge has created a demand for new technology solutions that can help balance the trade-off between current and future goals. IT leaders in manufacturing must avoid the beaten path of finding short-term fixes for increasing revenue; instead, they should look to long-term solutions that enable automation, enhanced use of data and improvements in customer experience. The Enterprise Cloud Index findings indicate that manufacturing leaders are aggressively adopting new technology to embrace modernization instead of getting left behind with legacy systems. The distributed cloud model offers a solution that delivers speed, flexibility, and localization, allowing manufacturers to improve efficiency without compromising quality.
While 91% of survey respondents reported hybrid cloud as the ideal IT model, today’s global average hybrid cloud penetration level is at 18.5% — the disparity due in part to challenges of transitioning to the hybrid cloud model. Manufacturing industries reported barriers to adopting hybrid cloud that mirrored global roadblocks, including limitations in application mobility, data security/compliance, performance, management and a shortage of IT talent. Compared to other industries, manufacturers reported greater IT talent deficits in AI/ML, hybrid cloud, blockchain, and edge computing/IoT.
Other key findings of the report include:
- 43% of manufacturers surveyed are currently using a traditional data center as their primary IT infrastructure, slightly outpacing the global average of 41%;
- However, manufacturers currently use a single public cloud service more often than any other industry. 20% of manufacturing companies reported using a single cloud service, compared to the global average of 12% — a testament to the fact that manufacturers are starting to turn to the cloud as a solution, given that they deal with legacy IT systems and cannot handle workloads on-prem;
- Manufacturers are also advancing the movement to private cloud: 56% of manufacturers surveyed said that they run enterprise applications in a private cloud, outpacing the global average by 7%;
- Manufacturers are struggling to control cloud spend. One motivation for deploying hybrid clouds is enterprises’ need to gain control over their IT spend. Organizations that use public cloud spend 26% of their annual IT budget on public cloud, with this percentage predicted to increase to 35% in two years’ time. Most notable, however, is that more than a third (36%) of organizations using public clouds said their spending has exceeded their budgets;
- Manufacturers chose security and compliance slightly more often than companies in other industries as the top factor in deciding where to run workloads: while 31% of respondents across all industries and geographies named security and compliance as the number one decision criterion, 34% of manufacturing organizations chose security and compliance as the top factor.
The bullish outlook for hybrid cloud adoption globally and across industries is reflective of an IT landscape growing increasingly automated and flexible enough that enterprises have the choice to buy, build, or rent their IT infrastructure resources based on fast transforming application requirements.
“Manufacturers are investing in modernizing their IT stack, and adopting industry 4.0 solutions to keep up with ever-changing business demands in areas like production and supply chain management,” said Chris Kozup, SVP of Global Marketing at Nutanix. “A hybrid cloud infrastructure gives manufacturers a fresh approach to modernizing legacy applications and services, enabling manufacturing IT leaders to focus on their long-term investments in big data, IoT, and next-generation enterprise applications. While the manufacturing industry is still facing obstacles in transitioning to multi-cloud use, this study shows us that manufacturing organizations are ready to accelerate growth and take the lead in IT innovation in the future.”
To create this report, Nutanix commissioned Vanson Bourne to survey more than 2,300 IT decision makers, including 337 worldwide manufacturing and production organizations, about where they are running their business applications today, where they plan to run them in the future, what their cloud challenges are and how their cloud initiatives stack up against other IT projects and priorities. The survey included respondents from multiple industries, business sizes and geographies in the Americas; Europe, the Middle East, Africa (EMEA); and Asia-Pacific and Japan (APJ) regions.
1 IDC FutureScape: Worldwide Operations Technology 2018 Predictions, doc #US42126317, October 2017
Jul 04, 2019 • Features • Artificial intelligence • Asset Maintenance • Homeserve
Will the asset eventually become more important than the engineer? It’s a question I put to most of the guests when I’m hosting The Field Service Podcast. As a journalist, I get a thrill of throwing a curve ball into interviews, and while it is often patted back with a straight bat by most; Paul Joesbury, Operations Director at utilities firm Homeserve is firmly on the side of technology. In fact, Paul is fought technology’s corner as part of a very juicy debate at Field Service Connect in May entitled, Today’s field service workforce will soon be redundant: The future lies in embracing technology to replace the need for human intervention when he went head-to-head with Anita Tadayon, Optimisation Director at British Gas, who argued for the engineer and technician.
Leading up to the event, I was fortunate enough to record a podcast with Paul where we discussed his views (It must be said at this point – and in the interest of journalistic impartiality – that Anita at British Gas was approached to also record a podcast, but her busy schedule meant it was not a possible) on the role of the human in future service. Straight away, I asked him if indeed, he felt there really would never be a case for human intervention in any area of service. “Certainly, from my perspective I can definitely concur,” he says confidently. “I do believe the asset will be more important than the engineer. I think assets are becoming smarter, I think we’re also seeing associated technologies, whether that be bots or something that’s aligned to the actual asset itself learning from each other.”
As a utilities company, Homeserve has the potential to lead the way in this type of service. “We’re doing a lot in water and boiler technology which I can definitely see it will tell us more about what the problems and faults are and will be less reliant on a human to come and do the diagnosis.” Paul explains.
He continues: “We’ve been having debates with our suppliers around use of drones to deliver parts, boiler diagnoses itself or what the problem is, then actually all we need is that part to be delivered and someone to fit it. It doesn’t need that highly skilled technician. Now obviously there may be certain appliances which do require a certain level of technical ability, however you could take it even further, when assets start fixing them themselves. Now that’s a really experimental concept,” he admits. “but there are things out there, nanobot technology for example, which is very, very clever.” When does he see this fundamental shift taking; where the human ceases to have a place in service? “I definitely think in five years’ time that there will still be humans in service but I think we’ll be doing different roles,” he predicts. “I think the important aspect over the next five years is to learn to trust the technology and equally for the technology to work.
But can the human ever truly be replaced? Surely face to face interaction is just as, if not more important? “Clearly there’s always the human empathy piece, that’s the bit that I haven’t yet seen any of this technology yet replicate to a high standard,” Paul admits. “I think there is still that human interaction. It’s different if you’re a lone worker fitting a part but certainly in our industry, the one I work in which is around going into customers’ homes, there is that empathy and there’s still a human approach to that, and I haven’t seen empathy replicated anywhere particularly well yet.
And perhaps this is where the rub lies and I’m in danger of opening up a bigger debate here beyond service; but nothing will ever truly replace the emotion of a human. That said, with self-driving cars around the corner nothing would really surprise me.
Jul 03, 2019 • News • future of field service • research report • Berg Insight • IoT • cellular
Growth was driven by exceptional adoption in China, which accounted for 63 percent of the global installed base. By 2023, Berg Insight's research now projects that there will be 9.0 billion IoT devices connected to cellular networks worldwide.
“China is deploying cellular IoT technology at a monumental scale”, said Tobias Ryberg, Principal Analyst and author of the report. “According to data from the Chinese mobile operators, the installed base in the country grew by 124 percent year-on-year to reach 767 million at the end of 2018. The country has now surpassed Europe and North America in terms of penetration rate with 54.7 IoT connections per 100 inhabitants.”
The Chinese government is actively driving adoption as a tool for achieving domestic and economic policy goals, at the same time as the private sector implements IoT technology to improve efficiency and drive innovation. Berg Insight believes that the role of the government is the main explanation for why China is ahead of the rest of the world in the adoption of IoT. Like other advanced economies, the country has widespread adoption of connected cars, fleet management, smart metering, asset monitoring and other traditional applications for cellular IoT. It has also given rise to new consumer services enabled by connectivity like bike sharing. The most distinctive characteristic of the Chinese IoT market is however the way that the government is systematically using new technology to implement its vision for urban life in the 21st century.
In the report, Berg Insight also analyses the IoT business KPIs released by mobile operators in different parts of the world and found significant regional differences. The monthly ARPU for cellular IoT connectivity services in China was only € 0.22, compared to € 0.70 in Europe. Global revenues from cellular IoT connectivity services increased by 19 percent in 2018 to reach € 6.7 billion. The ten largest players had a combined revenue share of around 80 percent.
Leave a Reply