Adopting IoT as part of the greater service and business environment involves keeping up with industry changes as they take place. That means incorporating better measures when needs arise in any business area and keeping cost-effective solutions in...
AUTHOR ARCHIVES: Field Service News
About the Author:
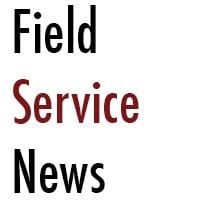
Field Service News is the world's leading publication for dedicated to the field service read by over field service professionals across the globe. If you are a field service practitioner you may qualify for a complimentary industry subscription - visit fieldservicenews.com/subscribe now!
Sep 25, 2018 • Features • Asset Management • Astea • Future of FIeld Service • field service • field service management • Internet of Things • IoT • Field Service Solutions • Service Management Solutions • WBR Insights • Managing the Mobile Workforce
Adopting IoT as part of the greater service and business environment involves keeping up with industry changes as they take place. That means incorporating better measures when needs arise in any business area and keeping cost-effective solutions in mind for future progress of the company as a whole.
Is IoT adoption a key topic for you?! There is a white paper on this topic available to fieldservicenews.com subscribers. Click the button below to get fully up to speed now!
sponsored by:
Data usage note: By accessing this content you consent to the contact details submitted when you registered as a subscriber to fieldservicenews.com to be shared with the listed sponsor of this premium content who may contact you for legitimate business reasons to discuss the content of this content.
Already, 76% of companies are using IoT data analytics to establish product and/or process quality imperatives. Their decision makers can analyze IoT data to improve solution recommendations, feedback on installations, demonstrations, specific services, and others.
IoT also serves as a signifier for opportunities to improve more processes, such as identifying popular products and managing inventory.
Respondents believe data should be usable in decision making at a variety of business levels. In every case, a majority of companies have either adopted IoT for specific business functions or plan to do so in the next 24 months. But companies prioritize customer-facing initiatives—service, products, and satisfaction—over internal functions such as business projections and aligning service data with financials.
Customer Satisfaction & Loyalty:
73% of companies have incorporated IoT (42%) or plan to do so within 24 months (31%) for the purpose of customer satisfaction and loyalty. More companies have incorporated IoT for this purpose than for any other measured in the study.
With connected data, companies are able to understand and fulfil customer demands better thanks to improved communication. In this way, minor technological improvements can be made without delay or other consequences.
Service Processes & Optimization
Respondents agree that connected data and IoT have helped streamline processes across departments. By leveraging IoT data, they can measure efforts for overall growth through set channels, be they internal or service-driven.
Now, 41% of companies have incorporated IoT for process optimisation, a close second to customer satisfaction and loyalty. Thirty-six percent have already incorporated IoT with service processes; more companies plan to do so within 24 months (37%) than with any other business function measured.
Product Uptime
Companies’ attention to customer experiences carries over to product support, where one respondent cites “notable improvements” to uptime in both industrial and consumer-driven channels. One healthcare executive says IoT helps them sustain products “during times of higher demands, especially due to the fact that these are used during medical procedures.”
More than one-third of companies have incorporated IoT for product uptime (34%); more than one-quarter of companies have plans to incorporate IoT with product uptime (30%) within 24 months.
Business Projections & Decisions
IoT data can be applied to various business requirements and provide essential statistics to support managerial functions. Derivations from reliable signals allow for better judgements when making business projections and decisions.
Over one-third of companies have incorporated IoT for business projections and decisions (35%); more than one-quarter of companies have plans to incorporate IoT with business projections and decisions (27%) within 24 months.
Predictive Maintenance
Respondents’ ambitions for better response to maintenance needs extends to real-time automated reporting, a better understanding of their products’ “general maintenance structure,” and even signals for customers to be proactive—to seek out maintenance themselves.
Several respondents cite their use of predictive reporting for scheduling, sustainability, and research methods, among others. Only 32% of companies have leveraged IoT for predictive maintenance; however, 29% plan to do so within 24 months.
Aligning Service Data with Financials
Fewer companies have incorporated IoT to align service data with financials (26%) than any other business function in the study. But the data suggests this is a growth area. More companies (61%) are either planning to incorporate IoT in this way within 24 months or are interested in incorporating IoT in this way than with any other business function.
Despite the prioritization of functions that drive customer success, it is in business projections, business decisions, and aligning service data with financials that companies take an increasing interest in incorporating IoT. At least one-quarter of companies have already incorporated IoT for each of these purposes.
Is IoT adoption a key topic for you?! There is a white paper on this topic available to fieldservicenews.com subscribers. Click the button below to get fully up to speed now!
sponsored by:
Data usage note: By accessing this content you consent to the contact details submitted when you registered as a subscriber to fieldservicenews.com to be shared with the listed sponsor of this premium content who may contact you for legitimate business reasons to discuss the content of this content.
Be social and share...
Sep 24, 2018 • Features • Augmented Reality • Future of FIeld Service • field service • field service management • Hololens • IoT • Service Management • Columbus UK • Microsoft HoloLens
Research indicates IoT deployments are set to skyrocket over the next four years, growing 140% to exceed 50 billion connected devices by 2020...
Research indicates IoT deployments are set to skyrocket over the next four years, growing 140% to exceed 50 billion connected devices by 2020...
As the cost and complexity of deploying connected devices continue to fall, IoT projects are no longer a far-fetched dream but a deliverable reality, already transforming a huge range of industries from Field Service to Manufacturing. Martin Clothier, Technical Director at Columbus UK, explains how businesses of all sizes can quickly seize advantage of IoT to deliver operational efficiency, provide actionable insights and improve business processes.
The Internet of Things has comfortably moved beyond the ‘hype’ stage of recent years, with IoT devices and projects now cheap enough to be viable for almost any business. Smaller IoT projects are capable of reaching full operational status in as little as a week. Deployments currently range in ambition from a dozen sensors to capture warehouse temperature, to monitoring the output and performance of remote oil fields across Africa.
There are more and more industries now taking advantage of IoT – and their success lies in identifying the right use case and ensuring they successfully harness device data to produce actionable insights.
Use Case One: Turning inefficiency into opportunity
The manufacturing industry is set to gain from IoT deployments that focus on using connected devices to provide a detailed, real-time picture of existing business operations and identify bottlenecks inefficiency. With repetitive processes running around the clock, any minor improvements to efficiency in the production cycle can generate major savings for a manufacturer.
"Identifying anomalies at an early stage can allow employees to take immediate corrective action to avoid excessive wastage, unnecessary asset strain or increased production cycle times..."
IoT sensors connected to machinery generate continuous streams of performance data, which can be analysed on platforms such as the Azure IoT Suite to identify leaks and bottlenecks hindering production. Identifying anomalies at an early stage can allow employees to take immediate corrective action to avoid excessive wastage, unnecessary asset strain or increased production cycle times.
This potential is not limited to minor efficiency improvements but can provide key metrics that drive business success. If we take, for example, the food and beverage sector – product quality is a top priority. Installing connected cameras above a production line enables manufacturers to introduce machine vision – monitoring and analysing the packaging, labelling and quality of products to ensure compliance and consistency.
Use Case Two: Space optimisation and the race against time
IoT monitoring is not restricted to simply monitoring and reporting physical asset conditions but can provide valuable insights into the two basic resources manufacturers have to juggle – space and time. At Columbus, we’ve worked to develop SpaceMAX that helps optimise usage of both workspace and time. With physical space at a premium for businesses – particularly in urban areas – optimised space usage can be invaluable in securing a competitive advantage.
Deploying connected beacons throughout a location such as a warehouse will capture the locations of assets, employees and vehicles from a forklift to a tow tractor. Harnessing the Microsoft Azure
platform, this location data can then be analysed to produce heat maps and identify hotspots, bottlenecks and other areas of inefficiency. By eliminating these we can optimise operations, product flow and the use of employee time.
Use Case Three: Tackling skills shortages by providing a helping hand to junior technicians
The threat of a skilled workforce shortage is well documented, with the UK cited as being particularly at risk. As the number of skilled engineers and field service technicians shrinks, the burden to complete detailed installation, repair and maintenance tasks falls increasingly on the shoulders of less experienced staff. Technology holds the answer to ensuring speed and quality is not compromised during remote site visits.
"The augmented reality aspect of the HoloLens can be harnessed to deliver contextual information such as service history and manuals explaining the maintenance process step-by-step..."
Here’s where developments such as the Microsoft ‘mixed reality’ HoloLens headset take centre stage. Using this headset senior workers can provide remote support and supervision for challenging maintenance tasks, tapping into a collaboration platform such as Microsoft Teams to discuss the task at hand. The augmented reality aspect of the HoloLens can be harnessed to deliver contextual information such as service history and manuals explaining the maintenance process step-by-step.
Remote assistance is just the first step for potential HoloLens applications. More advanced applications involve streaming real-time IoT data directly to the headset, such as telemetry of a production asset, assisted picking or put away, or projected life expectancy of individual components.
Bringing it all together – the icing on the transformation cake
By introducing connected devices to monitor environmental conditions, asset status and performance levels, we are generating significant volumes of data around the clock. But how can we translate data generated by machinery on the shop floor into actionable insights?
In order to make use of IoT data, businesses need to be able to collect, format and clean IoT data for analysis. Rules can then be set for actions to be taken if data falls outside of acceptable thresholds, such as staff being notified if a sensor detects a sharp rise in temperature. This is where cloud solutions come into play.
Cloud-based platforms such as the Azure IoT Hub introduce advanced machine learning tools to further identify complex patterns, and data visualisation for supervisors to closely monitor operational performance in real-time. By unlocking these previously unseen insights, IoT is enabling business leaders to make data-driven decisions to improve efficiency for the first time.
IoT can be also a significant asset to businesses by introducing increased automation of repetitive workflows – requiring just minor oversight from supervisors. Take field service as an example. Asset performance data from IoT sensors fed into the Azure platform can be analysed to detect anomalies, indicating a particular component is expected to fail shortly. Through a platform such as Dynamics 365 for Field Service, an automated work order can be created, scheduling an engineer to be dispatched with the correct component to complete maintenance before the failure ever occurs. This brings the added benefit of ensuring business processes are never brought to an unexpected halt through asset failure – an action which could cost thousands in lost revenue.
Staying ahead of today’s wave of digital disruption
The steady rise in successful enterprise IoT projects is testament to how IoT is today delivering on the promise of connecting people, processes and systems to enhance business operations and efficiency.
[quote float="left"]Businesses that have not yet developed an IoT strategy to enhance their operations are in danger of surrendering any competitive advantages developed through previous innovation.[/quote] Businesses that have not yet developed an IoT strategy to enhance their operations are in danger of surrendering any competitive advantages developed through previous innovation. But they must also be wary of avoiding the temptation of rolling out connected devices piecemeal, and instead opt for a comprehensive, measured IoT strategy that will consistently add value and deliver the in-depth business intelligence to make smarter decisions.
The real opportunities of IoT are often hidden in full view! Many businesses find it difficult to identify the areas from which they will gain maximum benefit and ROI. Partnering with an experienced company such as Columbus can provide a ‘third eye’, helping companies develop an IoT strategy, deploy suitable hardware and software with sufficient scalability, and support the project from planning stage through to go-live – and beyond.
Columbus is hosting an IoT Quick Start Workshop at the Microsoft HoloLounge in London, 2 October, to help organisations develop their own IoT proof of concept, break down existing use cases and identify operations where IoT can add value and provide actionable insights. Business leaders can secure their spot at the workshop by registering here.
Be social and share
Sep 24, 2018 • News • Aftermarket • copperberg • field service • Service Management • Parts Pricing and Logistics
As a cash cow of the service division, how prepared is your spare parts business to embrace increasing pressure from customer expectations, changing trade agreements, and intra-connected new technologies? How will these and more affect your parts...
As a cash cow of the service division, how prepared is your spare parts business to embrace increasing pressure from customer expectations, changing trade agreements, and intra-connected new technologies? How will these and more affect your parts pricing strategies, logistics network, and warehousing management?
If you can take this 3-minute survey to help us build an accurate picture of current industry sentiment and the key trends in this area it would be hugely appreciated. Please take a few minutes to take @ https://www.surveymonkey.com/r/parts2019
Upon closure of the survey, we will be working alongside Coppeberg who produce the excellent Spare Parts Business Forums both within the UK and Europe to create an ebook of the survey results, with expert commentary from industry insiders, as a benchmarking tool for you to evaluate the direction of your spare parts business - so take part now and keep your eyes out for this exciting forthcoming report!
Be social and share...
Sep 21, 2018 • Management • News • Augmented Reality • Nick Frank • field service • GE Digital • selling service • Service Community • Service Management • servicemax • MOD
Places for the upcoming Service Community event which is being hosted by GE Power, are now becoming very limited...
Places for the upcoming Service Community event which is being hosted by GE Power, are now becoming very limited...
The event will be hosted at Ge's state-of-the-art facility at Stafford on the 16th October from 11.00 to 16.00.
As one of the most sophisticated Buyers of Advanced services, Keith Rushton from the MOD will give unprecedented insight in how performance related services are purchased, and why the MOD has been so influential in developing the new BSI standard for Services. We have one of the best presentations on Selling Service Value I have seen from Leon Sijbers of GE Power and Ross Townsend from Ishida will be sharing their Service Transformation story. Phil Newton from BT will share his experience of rolling out an Augmented Reality Solution to one of the largest Field Service Organisations in the UK. And finally, Mark Homer from GE Digital will share some research on the importance of Service Data in industrial businesses.
The Service Community creates discussions and insights that are far deeper than most conferences, due to the informal and intimate nature of our events. This is because we are a community in the true sense of the word, run by volunteers, with no sponsors, no exchange of money, no legal entity no hidden agenda's, just real people talking about real things motivated by a desire to learn.
Please feel free to forward this information to colleagues who you think would be interested. We look forward to seeing you in October and remember to register by sending an email to info@service-community.uk . We will then contact you to confirm registration and will send out the joining instructions nearer to the event.
Be social and share...
Sep 21, 2018 • video • Features • Autonomous Vehicles • field service • Service Management • Driverless vehicles • Volvo Trucks • Parts Pricing and Logistics
Volvo Trucks has been using connectivity for many years to support customers with efficient service planning. Now technologies are opening up new opportunities to take truck uptime even further. Enabling a deeper, more thorough analysis in real time...
Volvo Trucks has been using connectivity for many years to support customers with efficient service planning. Now technologies are opening up new opportunities to take truck uptime even further. Enabling a deeper, more thorough analysis in real time so that we can predict some potential failures that may otherwise have resulted in an unplanned stop.
It is interesting for us in field service to monitor just how rapidly vehicle automation is moving forward in the logistics sector as it will surely translate from HGV to LCV soon enough and Volvo Trucks are currently pioneering in the field.
Be social and share...
Sep 20, 2018 • News • field service • field service software • Service Management • Software and Apps • software and apps • API • Integrations • Jonathan Eastgate • SimPRO • Wrokforce Management • Managing the Mobile Workforce
Web programmers and business managers across the United Kingdom will be able to integrate online applications faster and easier than previously possible thanks to a new API product released by global job management company simPRO.
Web programmers and business managers across the United Kingdom will be able to integrate online applications faster and easier than previously possible thanks to a new API product released by global job management company simPRO.
simPRO’s ‘RESTful API’ product was developed as a software interfacing tool which allows various systems to connect and communicate with a new sense of efficiency, strengthening the bridge between simPRO and other platforms which may be used in the workforce.
An Application Programming Interface, or API, is broadly defined as software that allows two applications to talk to each other, acting as a messenger to allow third-party developers to retrieve and insert specified data into that application.
The simPRO API allows for seamless integration of data between it and other business software platforms.
simPRO Chief Technology Officer Jonathan Eastgate said the simPRO RESTful API would ultimately lead to better software integrations and an overall increase inconvenience for businesses.
“simPRO’s new API is a technical step forward, but its functions are good for users because external applications can be created to move data between simPRO and different applications,” he said.
“With the API you can now create integrations that connect simPRO to mailing and accounting systems, ecommerce, business websites, smartphone and tablet apps and document management systems.
“Thanks to simPRO RESTful API, businesses are able to integrate simPRO and third party applications easier than ever before.
“That’s what we strive to do at simPRO – removing time and complexity from modern necessities like program integration and online product use. We want to empower our partners in the United Kingdom to build valuable businesses around the information flowing through simPRO.
“simPRO’s new API systems will assist in managing workflows and improving efficiencies for thousands of trade service businesses,” Mr Eastgate said.
simPRO’s RESTful API was designed to be up to date with industry standards and features a Developer Centre where users can receive support through a dedicated forum and access assistance resource like code examples and program walkthroughs.
The new API will be made available world-wide upon release and be functional through simPRO’s Service and Enterprise range, making it accessible for a diverse range of users throughout the trade service industry.
Be social and share...
Sep 19, 2018 • Management • News
Juniper Networksan industry leader in automated, scalable and secure networks, today announced it has expanded its 18-year partnership with Ericcson a global leader in mobile networks, to deliver a comprehensive end-to-end 5G solution leveraging...
Juniper Networks an industry leader in automated, scalable and secure networks, today announced it has expanded its 18-year partnership with Ericcson a global leader in mobile networks, to deliver a comprehensive end-to-end 5G solution leveraging each company’s complementary portfolios. Together, the companies are now offering service providers a complete 5G transport network solution with a single pane of glass visibility to manage the new requirements of next-generation mobile service delivery.
This deepened partnership aims to offer service providers a complete solution from radio to core for new-service delivery while managing mounting complexity. 5G is expected to be a game changer for the next generation of business and consumer services, but the increase in connectivity, network traffic and customer expectations will likely create new challenges for managing the mobile transport network in a cost-effective way.
"5G is expected to be a game changer for the next generation of business and consumer services..."
Evolving 5G use cases, including connected cars, AR/VR and 8K video streaming, and the associated 5G radio requirements needed to support these diverse applications can place additional demands across the network. Capacity, connectivity, latency, synchronisation, reliability and security needs will all require tighter integration between the 5G radio, core and transport layers of an end-to-end mobile network.
To alleviate these challenges, Juniper’s expanded partnership with Ericsson greatly simplifies service providers’ 5G transformation by creating a tightly integrated solution that combines Juniper’s routing for next-generation WAN services and IP transport, and Ericsson’s Router 6000 and MINI-LINK microwave portfolio for distributed, centralised and virtualised radio access. In addition, the solution leverages Juniper’s Unified Cybersecurity Platform to secure the entire 5G mobile infrastructure against ever-expanding and sophisticated threats. This comprehensive solution provides seamless connectivity from the radio cell site to the mobile core all unified under Ericsson’s management and orchestration solution, improving the performance, quality and ease-of-use of the entire 5G solution. The joint end-to-end 5G transport solution will be designed and built from day one with the intent of supporting exceptional 5G radio performance in a cost-effective way.
As part of this deepened partnership, Juniper will utilise Ericsson’s go-to-market for mobile opportunities and Ericsson will include Juniper’s solutions for edge, core and security as part of its end-to-end 5G transport portfolio.
Be social and share...
Sep 18, 2018 • Management • News • B2M • field service • Service Management • Mobile Impact • Worker WElbeing • Managing the Mobile Workforce
New research released recently shows that mobile device reliability is having an enormous impact on the health and well-being of mobile workers, with over 40% experiencing stress or anxiety due to device issues that prevent them from completing...
New research released recently shows that mobile device reliability is having an enormous impact on the health and well-being of mobile workers, with over 40% experiencing stress or anxiety due to device issues that prevent them from completing their job effectively.
The strain of dealing with device issues in the field, such as battery failure or crashing apps, led to 16% of mobile workers taking at least one day off work in the last year due to the resulting stress or anxiety, including 7% who took six or more days sick leave as a result. As well as being unable to complete tasks, respondents also said mobile device failure sparked customer anger and rudeness, further increasing stress and anxiety levels.
When the findings are applied to the entire UK mobile workforce, estimated at 12,596,000 people, the cost of sick leave taken as a result of stress or anxiety caused by device reliability issues to the UK economy would be at least £1.18bn per year. Added to the US research results, the economic impact on both economies would be at least £7.9bn.
[quote float="left"]29% said they suffered stress or anxiety as a result of mobile issues but hadn’t taken time off as they could not afford to[/quote]A further 29% said they suffered stress or anxiety as a result of mobile issues but hadn’t taken time off as they could not afford to. Additionally, 24% said they haven’t raised their device issues to management as they felt their employer will not do anything about it.
The figures are the result of a survey of mobile workers in the UK and US by B2M Solutions, a global software company that dramatically improves how enterprise mobility is operated and managed.
The ‘Mobile Impact Survey’ took the opinions of 200 mobile workers across the UK and US who stated that the mobile device they used at work was a critical tool for them to complete their tasks, and that device reliability was paramount.
The impact to businesses for the time that staff take away from work increases the Total Cost of Ownership of mobile devices, the typical metric for measuring return on investment, by up to 14% per year. B2M states this is a key component in deriving the True Cost of Ownership™.
Gary Lee, B2M Chief Revenue Officer, commented: “Businesses are placing more responsibility onto their mobile workers but aren’t investing in tools to ensure the critical mobile devices they need to perform these new tasks are operating correctly and can be depended on.
“And it’s in their own interest. Our estimates on the cost of device failure are conservative, as even our True Cost of Ownership figures do not include further potential impacts such as having to pay overtime to remaining workers to pick up their sick colleagues’ excess work, financial penalties for missing customer SLAs, brand reputation damage, insurance claims or in extreme cases the cost of out of court settlements for workers who are unable to return to work.”
Be social and share
Sep 17, 2018 • News • Blockchain • deloitte • Business Ecosystems • Citizens Reserve • Eric Piscini • SUKU • Parts Pricing and Logistics
Citizens Reserve, the high tech startup led by several entrepreneurs and former Deloitte blockchain executives, has unveiled SUKU, an industry agnostic supply chain solution aimed at tackling the issues of transparency, efficiency, and product...
Citizens Reserve, the high tech startup led by several entrepreneurs and former Deloitte blockchain executives, has unveiled SUKU, an industry agnostic supply chain solution aimed at tackling the issues of transparency, efficiency, and product visibility in legacy systems.
A blockchain-based platform, SUKU expects to open new markets, improve operations and reduce the cost of running supply chains. The SUKU ecosystem intends to provide key advantages to trading partners such as access to real-time, transparent data around the precise location of goods, the privacy of partners, a bid and order marketplace, auditability of activities and the automation of contractual agreements.
Eric Piscini, Citizens Reserve CEO, said, “The current supply chain environment is complex and difficult to navigate. Almost all enterprises require a supply chain to some extent, but the technology supporting them remains expensive, inefficient and fragmented. With SUKU, we’re planning to build the decentralized supply chain as-a-service platform that can span across industries, enabling our trading partners to interact in a way that’s been all but impossible up until now.”
"With today’s businesses often working with myriad partners on a global scale, the challenges presented by supply chain management are increasingly vast..."
With today’s businesses often working with myriad partners on a global scale, the challenges presented by supply chain management are increasingly vast. Whether locating a Chinese supplier or finding a carrier to haul products from LA to Toronto, these challenges are amplified by the lack of one global governing body or a set of standards to ensure end-to-end visibility.
Eric Piscini said, “Recent contentious incidents such as the Chinese pharmaceutical scandals have showcased the need for one layer of connection for trading partners to communicate and transact. From hardware to energy, all industries utilizing a supply chain take risks working with untrusted partners. The true value of a decentralized ecosystem comes in its nature of being trustless and having no single point of failure.”
SUKU’s unique ‘supply chain-as-a-service’ concept expects to eradicate the three primary obstacles in supply-chain by providing visibility of products, access to capital and innovation, and engagement between stakeholders. In order to bring greater visibility to the supply chain, SUKU aims to display the precise location and status of goods in real-time, which is essential in ensuring that all parties can act proactively, instead of reactively when an issue arises.
The platform anticipates to provide companies with access to new marketplaces and technologies, and better connect suppliers, manufacturers, distributors, and retailers.
Designed to be industry-agnostic, from farming to pharmaceuticals, to electrical goods, the SUKU platform anticipates the use of two blockchains, Ethereum and Quorum, to maximize the benefits of both networks. The public Ethereum blockchain used extensively for smart contract deployments, is expected to handle supply chain payments.
The permissioned Quorum blockchain aims to facilitate transactions such as bids and offers, where confidentiality is critical. SUKU’s native token is necessary to incentivize and reward partners of the platform.
The platform’s built-in transparency and auditability also project to empower more socially responsible practices amongst trading partners by providing greater awareness about the provenance and origin of goods, as well as the values of the organizations they work with.
Be social and share
Leave a Reply