Additive Manufacturing (AM) is on the front line of the unfolding industrial revolution. This string of rapid prototyping technologies is replacing conventional production, and consequently, it is poised to generate substantial economic revenue by...
ARCHIVE FOR THE ‘additive-manufacturing’ CATEGORY
Apr 20, 2020 • Features • 3D printing • copperberg • manufacturing • Additive Manufacturing
Additive Manufacturing (AM) is on the front line of the unfolding industrial revolution. This string of rapid prototyping technologies is replacing conventional production, and consequently, it is poised to generate substantial economic revenue by 2035—$196.8 billion. Adrian Cirlig and Teodora Gaici explain more...
The future is certainly bright, but so is the present. On any given day, manufacturers can turn to AM technology to facilitate the production of individually customized products at relatively low costs, reshape the design process, and consolidate their supply chains.
AM will remain a particularly active architect of customer-driven design, virtual inventory, and rapid iterationsfor new product development. Yet it’s not all roses; the lack of quality consistency may slow production runs to a trickle.
In consequence, is AM both the cure and the culprit of innovation volatility? Industry experts seem undecided in the matter as this paper from the Rand Corporation outlines.
Additive Manufacturing: A Magic Bullet for Field Service Logistics?
AM is, after all, a disruptive technology—one that comes with a learning curve. Many top-tier leaders have justifiably gauged the trajectory of additive technology, and when they sensed it had promise, they gingerly lunged for it.
Through the use of AM technologies,anyone can manufacture products without any required tooling for production. That’s right—traditional molding techniques or large machines that have yet to be deftly transported will no longer impede manufacturing performance. Simply put, this set of powerful AM machines has the ability to fabricate a product from a digital geometry representation. Once they accurately replicate computer-aided design drawings, AM tools directly transform three-dimensional structures into functional physical prototypes and, more recently, ready-for-use products—all that in just a matter of minutes. The physical parts are built out of plastics, polymers, metals, ceramics, stainless steel, or other types of material by using a layer-by-layer printing process. A vast majority of modern AM machines print with multiple materials simultaneously and allow the development of mixed-material products.
"Manufacturers must have a plan for everything—how, when, and where they design and manufacture products rank top of the list..."
Organisations with a strong innovative culture recognize the need to facilitate on-demand production, and as it turns out, they’re growing faster and increasingly outpace their competitors.
Innovation, however, is rarely linear. In most cases, it’s a progressive affair that disrupts practically every aspect of the business
Manufacturers must have a plan for everything—how, when, and where they design and manufacture products rank top of the list. AM is already distorting modern-day manufacturers’ long-planned reality by encouraging them to rethink every design-to-fabrication procedure and go well beyond traditional manufacturing methods. Those who are up to the challenge will become the leading innovators in their market.
Additive Opportunities for the Taking
The revolutionary AM technology is becoming commonplace one layer at a time.
This significant surge in popularity may be due to the proposed benefits that are in visible contrast with those provided by conventional manufacturing operations.
Milling, for example, can produce a large amount of unnecessary material waste. Distinct in nature, additive processes have become a statement of sustainability—both economically and environmentally. It is touted that AM technology reduces energy consumption, facilitates dematerialisation, and improves resource efficiency by using waste as an input to construct equitably personalised products in a cost-effective manner.
This type of manufacturing process also attempts to minimise the need for packaging, transportation, and storage. More than that, prototyping and building a high-value product from geometrically complex data in-house can also significantly reduce shipping costs and shorten supply chains.
Since AM machines offer complete (and highly flexible) design freedom, they allow early customer involvement in the product development process. This customer-driven design procedure helps manufacturers respond to individually customised demand wherever needed, revise and conduct timely design changes, and reduce time-to-market. Above all, manufacturers are empowered to forge direct-to-consumer relationships and prolong the lifetime value of a specific object.
"With large-scale printers being well underway, Additive Manufacturing technology will steadily extend its capabilities..."
It’s impressive, but that’s just barely scratching the surface. AM is an advocate of product differentiation—at scale!—and industry experts can take full advantage of this technology to mass-produce custom-fit objects without paying a steep price for additional workers or tooling. Manufacturing in large volumes will, in fact, reduce the cost per unit, minimise the total cost of ownership, and drive greater growth.
At the moment, AM machines can mainly print tiny (yet rather complex) items; they can briskly produce fully-functional parts in just a single production step and without the need for assembly lines. With large-scale printers being well underway, AM technology will steadily extend its capabilities to open up innovative business models across the industry.
Additive Manufacturing Technology Is Ripe for Investment, But the Caveats Remain
It’s in the cards: AM tools will offer unlimited design-to-fabrication opportunities for modern-day manufacturers. The vast majority of these professionals may inevitably face certain drawbacks that can’t (and most probably won’t!) go unnoticed.
Quality consistency is one of the main stumbling blocks.
Every manufacturer aims to develop consistent parts and ensure repeatable quality levels throughout their production lines. Yet no two items are exactly the same. Given that AM machines can produce parts as small as 500 nanometers, the differences may be slim or less obvious; but they exist, and a single inconsistent subset that is left unaddressed could put the brakes on the production line.
All the materials used for crafting AM-produced components should also be processed within the required quality standards and specifications, or else they might prevent objects from being recycled
"Many manufacturing and field service professionals haven’t gained an in-depth understanding of Additive Manufacturing techniques yet, let alone hands-on experience.."
The knowledge gap is another considerable barrier to the adoption of AM technology. As this study warns “[the] knowledge of AM in the industry exists in pockets.” Many manufacturing and field service professionals haven’t gained an in-depth understanding of AM techniques yet, let alone hands-on experience.
Amid global economic unrest, the lack of know-how may drive economic insecurity and hamper technology adoption.
Route Around the Gaps and Fortify Additive Manufacturing Innovation
An AM-produced component may be a sure bet for unprecedented manufacturing gains. That is, of course, if manufacturers do not band-aid the inevitable caveats that eagerly come with every disruptive technology. /p>
As AM technology advances, the trick is to promptly address each limitation or potential risk and transform every temporary hiccup into an opportunity for modernisng manufacturing lines.
Capturing AM’s transformative potential is crucial for manufacturers who want to advance customer-led product development and freely reach all their revenue growth targets.
Further Reading:
Adrian is the Editor for a series of key industry events with Swedish Conference Producer, Copperberg.
- Find out more about his forthcoming event the Field Service Forum @ https://www.copperberg.com/fieldserviceforum/
Nov 15, 2019 • Features • 3D printing • future of field service • Additive Manufacturing
Mike Shields, Technical Director at DMS Systems Ltd and Centrex Print Services brings us an in depth look at the potential power of 3D printing across multiple sectors...
Mike Shields, Technical Director at DMS Systems Ltd and Centrex Print Services brings us an in depth look at the potential power of 3D printing across multiple sectors...
Jun 04, 2019 • Features • 3D printing • manufacturing • Additive Manufacturing • Parts Pricing and Logistics
An industrial products manufacturer has a large portfolio of spare parts in its portfolio. It has 10 year service contract with its customers implying that the company must be able to deliver spare parts on time for 10 years to its customers even though the product may longer be produced. Thus, the company has to maintain inventory of some of those spare parts. Such inventory costs run into millions of dollars. Many of those spare parts are produced by suppliers. Demand for those spare parts are low and unpredictable.
On Monday morning, the spare parts manager received a call from a customer in another continent “ Mr. Paul, our equipment is out of action as it cannot be started in the morning shift. My maintenance guys confirmed we need to replace a part, supplied by you and we do not have it in inventory. I am sending you the part number. Please deliver it within three days otherwise there will be heavy loss.” Mr. Paul checked the part number in the ERP and found that they also do not have in stock.
He found out who the supplier is and called him up. The supplier replied saying that they cannot make only one piece. They will need an order size of at least 20 and it will take 1 week. What will Mr. Paul do? He remembered that the Vice President (VP) of Supply Chain was talking about 3D Printing of spare parts in the last meeting. Can the part be printed? How will Mr. Paul figure that out?
He refers to the presentation by VP- Supply Chain and finds the name of a company called 3D Hubs (UPDATE: 3D Hubs is now Hubs). Mr. Paul checks out the website of 3D Hubs and found that he can upload the drawing of the parts and get an analysis for printability along with a quote. He uploaded the drawing, got the quote for delivery within three days and went to his boss.
His boss, Mr. James said “Are you crazy? How will I be able to justify that price? Also, have you noticed that they are not printing our part using our specified material? This will never work.” Mr. Paul tried to argue “This is a very strategic customer for us. If they are not satisfied and cancel the service contract, it will be a big trouble for us. We can say that they can run their equipment with it until an actual replacement spare part is produced and delivered by the supplier. I can talk to R&D about the approval for the deviation in material. It doesn’t seem to be a big change.” Mr. James said “You are taking a big risk, Paul. If you want to try, go ahead.”
In the end, everything turned out well. That part was produced using additive manufacturing (AM) and delivered on time. Paul received appreciation for his efforts. VP- Supply Chain was very happy and said to Paul. “Now, I want to evaluate our entire spare part portfolio and develop a systematic process of evaluating which of those parts can be printed and which cannot. It will be great if you can evaluate our portfolio and present in our next month’s meeting.”
Paul has 10 years of experience in spare parts but he does not know much about 3D Printing. How can we help Paul? I am sure that there are many people like Paul in large industrial manufacturers, who need similar help. Lets try to outline a steps-by-step process for selecting spare parts suitable for additive manufacturing.
Step 1: Identify the objectives
Some potential objectives for producing spare parts using AM can be:
• Supply risk reduction;
• Lead time reduction;
• Inventory cost reduction;
• Ensuring local content;
• Minimizing loss of production;
• Reducing carbon foot print across life cycle.
Companies can decide the most relevant ones from those and provide relative importance of those using a method called analytic hierarchy process. Instead of directly assigning importance weights to each objective, experts within the company can make pairwise comparison of the objectives using a scale (for example 1-3-5-7-9) and derive the importance weights.
Step 2: Identify the factors to be used for screening the spare parts for AM suitability
Some factors, which can be used for screening the spare parts for AM suitability can be as follows: It is important to note that the company should have data on the following factors to be considered for screening.
If such data is not available or available in different IT systems or in physical form ( i.e. drawings with dimensions and material specifications), it will be difficult to include those at the screening stage.
1)Demand and demand uncertainty of the parts
Parts with low and uncertain demand are more suitable for spare parts
2) Overall part size
(Part must fit build volume of the equipment) As the equipment for different AM technologies have build size restrictions, part-size is usually a restriction, if it cannot be fitted in the build chamber. Sometimes changing the orientation of the part may be needed to fit it into the build chamber, but it might require additional support structures and may increase the overall production time. Decisions about part orientation in the build chamber can be taken only for the selected parts and not at this stage. The company can specify the upper limit of size or a range of sizes of parts, which they would like to consider
3) Materials
Not every material can be printed. Thus, parts whose specified materials can be printed can be screened when a company is starting on its journey of producing spare parts using AM. Later, alternate materials which closely match the specifications can be explored.
4) Supply lead time
Parts with long supplier lead time for conventional manufacturing can be more suitable for producing using AM as overall lead time can be reduced. A company may decide to specify either the lower limit or range of lead time, which they would like to consider.
5) Purchase price or unit cost
High priced parts, in general, can be suitable for AM but some high valued parts may be infeasible because of their size or materials etc.
6) Value of inventory across all locations
Usually parts with high inventory value can be good candidates to be produced using AM. High value of inventory can be due to high number of parts in stock or due to high prices. Sometimes, if a lot of stock is available, a company may decide not to proceed with producing such a part using AM. Some other company may decide that they would like to get rid of that stock and hence it may be worth producing those using AM. A company may also decide to include either price or inventory value as a screening factor.
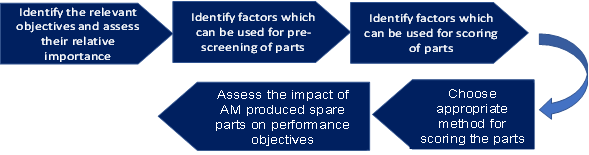
Figure 1: Step-by-step approach for selecting spare parts suitable for AM
Step 3: Identify the factors to be used for scoring the spare parts for AM suitability
Some potential factors for scoring spare parts in terms of their suitability for AM can be as follows:
• Lead-time;
• Unit cost;
• Criticality in terms of influence of the part for equipment shutdown;
• Demand predictability measured as standard deviation of demand;
• Supply risk in terms of number of suppliers;
• Minimum order quantity.
The screened parts can be scored based on the above factors and how the factors are related to the objectives. Parts with long lead time, high cost, high criticality, low demand predictability, high supply risk and high minimum order quantity in the existing manufacturing process will be more suitable for AM.
Step 4: Choose appropriate method for scoring the parts
There can be multiple approaches to score the spare parts in terms of suitability to be produced using AM.
We mention some basic guidelines below:
1. Multi-criteria decision making approach (MCDM) –scoring parts on factors and linking factors to be objectives (suitable for less number of factors and less number of parts).
2. Logic decision diagrams, cluster analysis and fuzzy inference system (suitable for large number of parts, medium number of factors but strong interrelationships of factors and objectives). If the factors are dependent on each other and how they influence the objectives depends on the levels of the factors i.e. low, medium and high, logic decision diagrams can be built to score a part using different decision rules. In terms of disagreement between experts about the relationships, the relationships can be expressed as fuzzy numbers and fuzzy inference system can be used to score the parts.
3. Cluster analysis and MCDM approach for ranking of part clusters and within cluster ranking of parts (large number of diverse parts, limited to medium number of factors and independence of factors) If the factors considered are independent but the spare parts portfolio is very diverse, it will be necessary to cluster the parts, rank the clusters and then rank the parts within the clusters.
4. Bottom-up expert driven selection using a questionnaire or selection protocol (no data available or not possible to do quantitative analysis) If no data is available in digital form to score the parts, it is prudent to use the expert judgment of the service personnel or maintenance technicians. But, as those persons may not be aware of AM technologies, it is important to demonstrate to them what is possible using AM through workshops and ask them to suggest spare parts, which they find most difficult to get. Companies can also potentially run internal competitions to identify some spare parts to start with.
Step 5: Assess the impact of AM produced spare parts on performance objectives
Once some spare parts are identified, the next step is to develop business cases for the parts. But, those can be done once the appropriate technologies and equipments are identified. For that purpose, a database of all available AM equipments, the technologies they use, the materials they use, the build chamber of the equipments, the surface finish achievable need to be documented.
For the spare parts which are scored high in terms of their suitability for AM, the most appropriate technologies and equipments can also be shortlisted. Then total-cost of ownership based cost models need to be developed to understand the economic implication of producing the parts using AM. The relevant cists which need to be considered are materials, production, energy, labour as well as the savings in inventory and transportation costs over the lifecycle of usage of the parts for different demand scenarios.
Quotes from different service providers can also be used as a reference for taking the final decision. Once a company has done this exercise and identified a few feasible parts, some machine learning techniques can be used to identify the patterns amongst the most suitable parts so that the process can be automated when new parts are added to the portfolio.
Leave a Reply